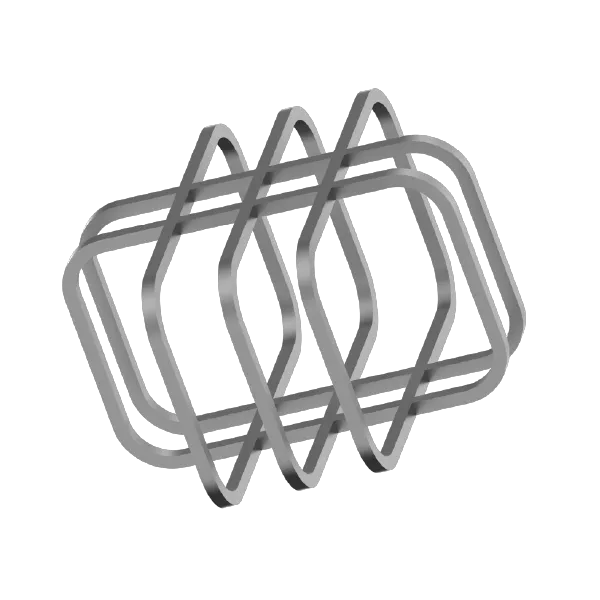
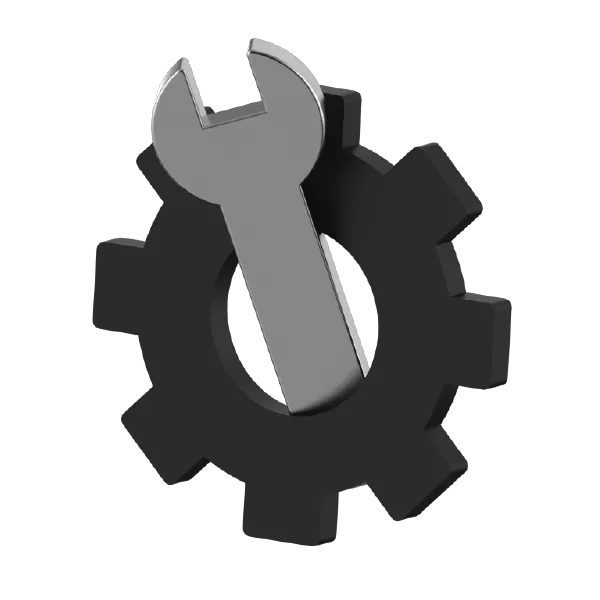
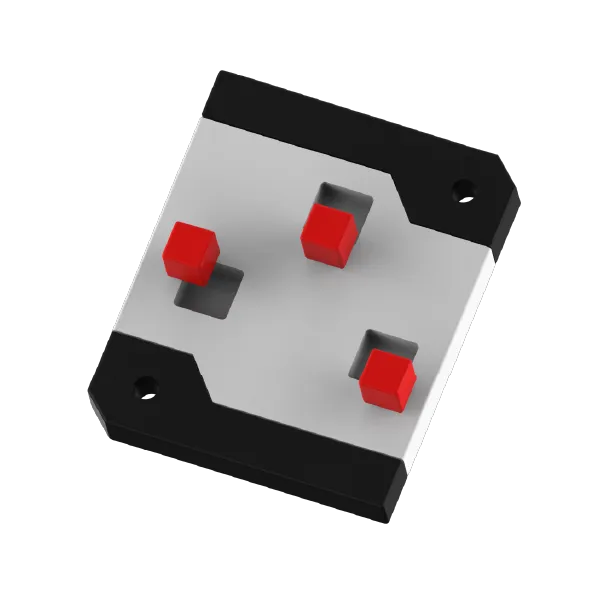
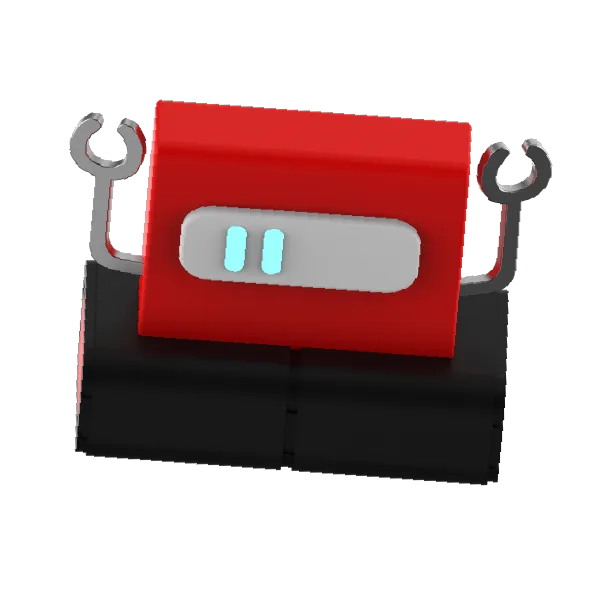
Advanced Design and Fabrication
Digital Test of Concrete Strength Development in Precast Production
Background and Current Practice
When carrying out concrete works in a precast plant, especially in an Integrated Construction and Prefabrication Hub (ICPH) where a Just-In-Time (JIT) manufacturing principle is adopted, it is important to ascertain the early-age strength development of the concrete. This is because components can only be demoulded if and when the minimum strength has been attained. This is usually measured using the conventional concrete cube testing method. Additional concrete cubes are also made to be sent to the relevant authorities for later-age strength measurement.
Concrete cube testing is a manual and laborious method. The test also results in a lot of waste as the crushed concrete cubes from the compressive load test will be discarded.
The results from the concrete cube test are often not an accurate representation of the actual state of the precast components due to the differences in curing conditions. Concrete in small cubes has the tendency to gain strength at a slower rate than the precast components that are larger in size. Thus, there are missed opportunities to demould the precast components earlier and have a faster delivery schedule.
Opportunity Areas and Key Challenges
We are interested in concrete sensing technologies that can measure the real-time strength development of concrete with minimal wastage of materials. Strength development of concrete could be inferred by analysing internal temperature changes of concrete to understand the chemical reactions that have taken place.
A new testing approach could reduce or eliminate the need to carry out the conventional concrete cube testing method. It also boosts production efficiency by giving real-time insights into the concrete structure, so that it can be demoulded as soon as the minimum required strength is attained.
The test will be conducted on flat slabs produced in the ICPH. The solution could be based on different sensing approaches, but need to consider the following requirements:
- The sensing technologies must work for precast elements with thickness of 70 to 90mm. Ideally, the technology can work for thicknesses of up to 150mm.
- Embedded sensors must be small enough to be placed within the rebar structure of the precast components.
- Embedded sensors should ideally operate wirelessly so that there is no additional effort required to find the sensors.
- External sensors must be able to accurately identify the internal conditions, for example, the temperature of the precast element.
- The solution must have a low implementation cost that amounts to <1% of the total component raw cost.
- The solution should consider the concrete strength development benchmarks according to EN206 and other relevant standards set by local authorities.
The solution must include a tablet-friendly digital platform that integrates and visualises the data from the sensors, and produces insights and alerts that can be easily understood by the on-site workers.
Expected Outcomes
The concrete sensing technology accurately measures the real-time strength development of precast flat slabs, so that the demoulding can be done at the best time to increase production by at least 25% and reduce the risk of defects caused by demoulding before the required concrete strength is attained.