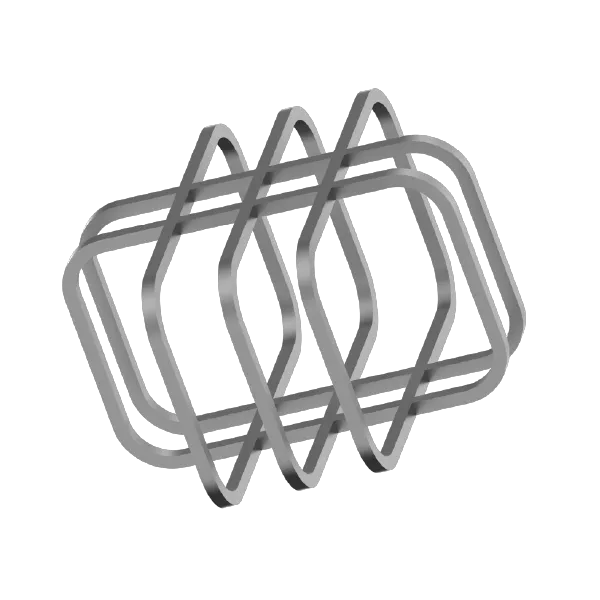
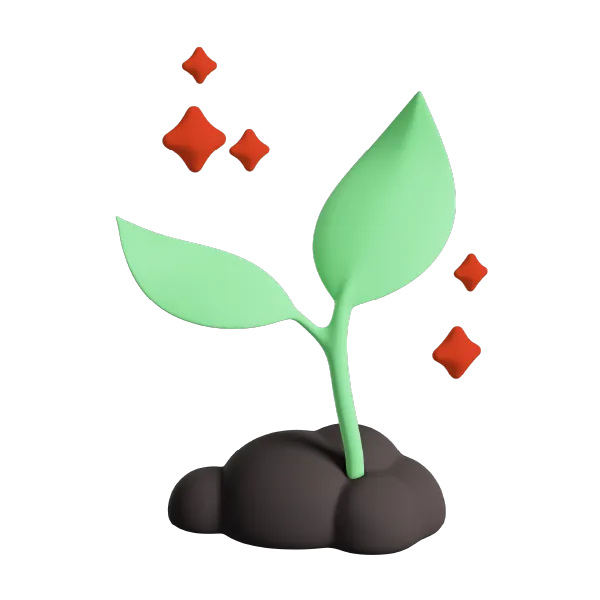
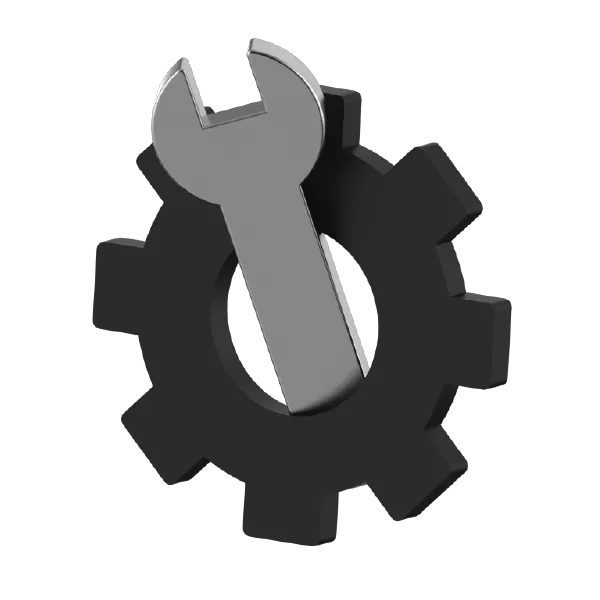
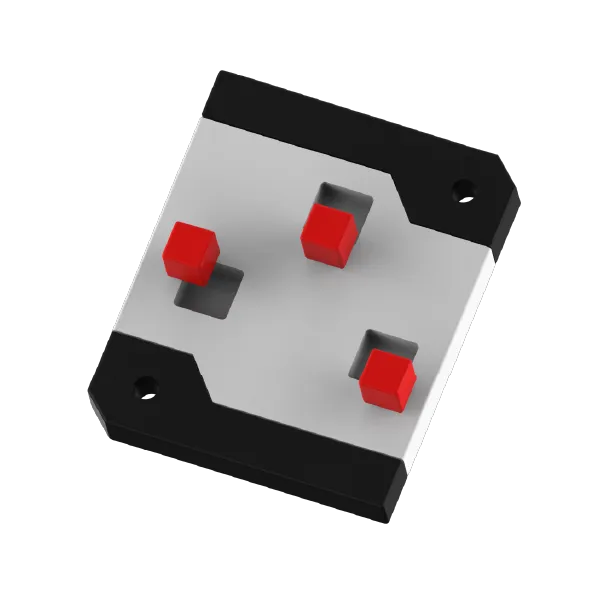
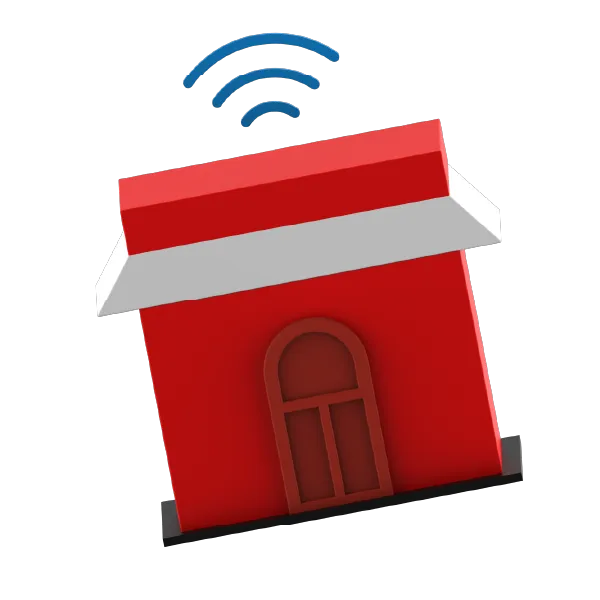
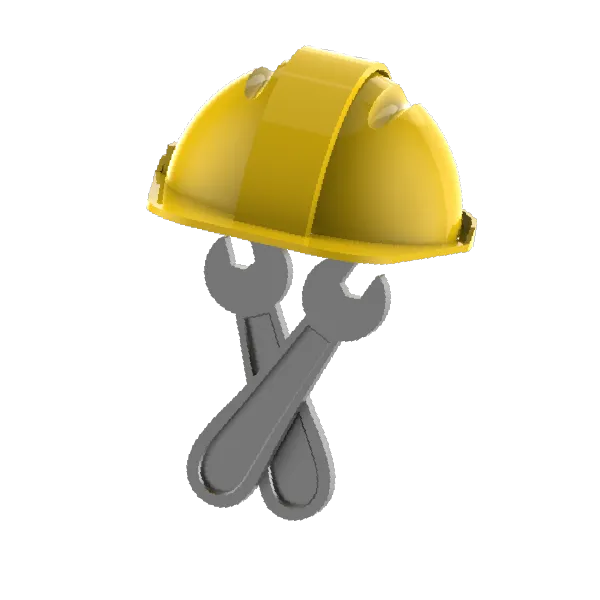
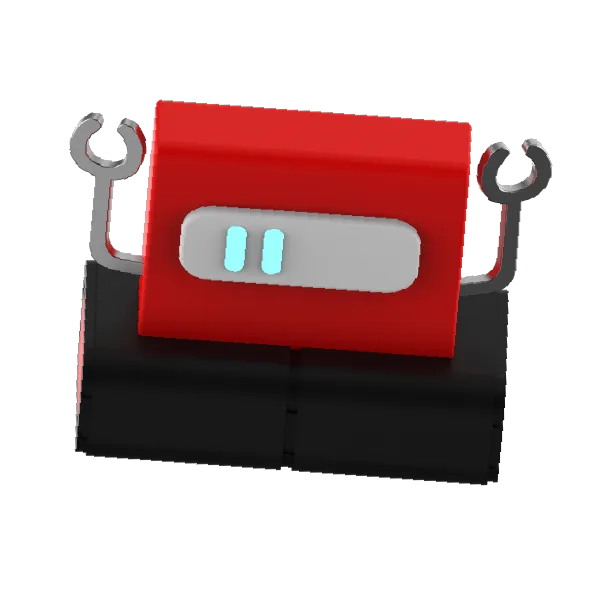
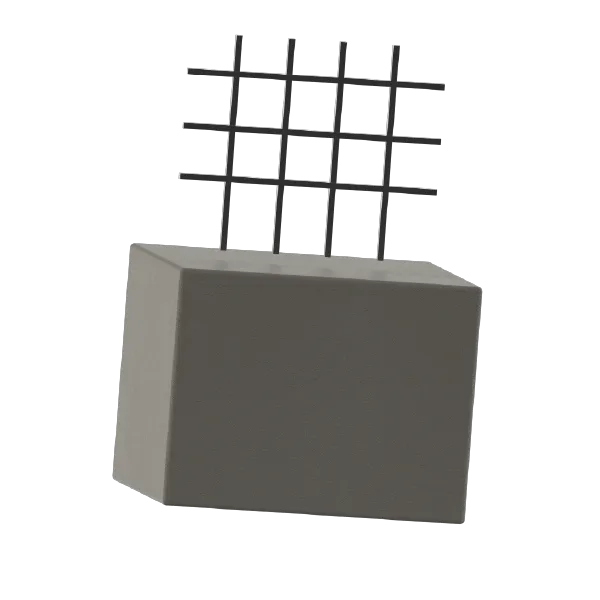
About Us
Programme Overview
Objectives
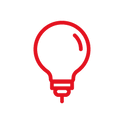
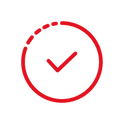
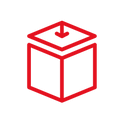
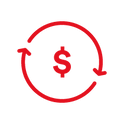
Thematic Pillars
Past Challenge Statement
Robotic Painting of High-Rise Building Façades
Challenge Area
Challenge Statement Owners
Current Situation
Painting works on external walls of buildings are usually carried out using rollers and brushes. To work on high-rise buildings,workers are hoisted on suspended scaffold gondola systems. Despite stringent safety protocols, the inherent risks of working at considerable heights. If the safety procedure is not followed properly, or if an unexpected equipment malfunction occurs, a serious accident may result.
Additionally, it is becoming increasingly difficult to recruit workers, resulting in a manpower shortage. It is thus becoming necessary to look into ways to reduce reliance on manual labour for building painting works.
TMS Alliances would like to explore robotic solutions to replace current conventional painting methods that require the use of gondolas or other hoisting equipment. Such a system can significantly decrease the need for human workers to be exposed to the dangers of working at height. By automating the painting process, the reliance on manual labour can be reduced.
Also, robots can paint large surfaces more quickly and consistently than human workers, potentially improving the efficiency of painting projects. They can be programmed to apply paint with precise control over thickness and coverage, leading to a higher quality finish. They may even navigate complex environments and overcome obstacles that would pose challenges to human workers.
Challenge
TMS Alliances is looking for a robotic solution for the painting of external walls of high-rise buildings.
Expected Outcomes
The solution should:
- Negate the need to use gondolas, boom lifts, and other work-at-height equipment;
- Be able to operate unpiloted during the painting process;
- Be compatible with currently available painting materials and technologies;
- Be compatible with building mapping standards (for example, DJI Mapping and BIM) to enable automated painting;
- Enable paint to be applied to at least 80% of external walls;
- Enable paint to be applied without contaminating the surrounding environment (that is, no overspray); and
- Achieve improvement in productivity by 50% compared to conventional methods.
Good to have:
- Be able to apply paint to hard-to-reach surfaces or corners.
Past Challenge Statement
Robotic Concrete Slump Testing and Cube Making
Challenge Area
Challenge Statement Owners
Current Situation
The slump test is a basic quality control test that determines the workability of fresh concrete. Cube making is a method to determine the compressive strength of hardened concrete. Both are essential to ensure the high quality of concrete used in construction projects.
The current practices in both are time-consuming and labour-intensive. Further, the manual nature of these tests means they are prone to human error and can be affected by factors, such as the skill and concentration level of the operator. These inconsistencies can result in problems, as it is critical for testing methods and measurements to exactly align with the EN standard. Additionally, it is becoming increasingly challenging and expensive to hire skilled workers to perform these tests.
There have been some studies done to tackle these challenges, including the use of digital measurement and data processing for slump testing, but no integrated solution has been developed so far. With the increasing demand for sustainable and efficient construction practices, Pan-United sees an opportunity to explore automated solutions for slump testing and cube making.
Challenge
Pan-United is looking for a robot-assisted solution that can perform concrete slump testing and cube making accurately and efficiently.
Expected Outcomes
The solution should:
- Complete the process within a reasonable time;
- Be portable and thus easy to transport to different sites;
- Require minimal training to use, making it accessible to a wide range of users;
- Require minimal manual intervention;
- Result in cost savings in terms of time and manpower;
- Be able to operate in environments with: some text
- Shaded temperature of 20-40°C
- Humidity of 50%-90%
- Minor levels of dust
- Minor levels of moisture
- Be energy-efficient; and
- Produce minimal waste and emissions.
Specific for slump testing:
- Perform concrete slump testing accurately according to EN 12350-2 and EN 12350-8 standards; and
- Auto-measure the slump and slump flow of fresh concrete with minimal error.
Specific for cube making:
- Perform cube making accurately according to the EN 12390‐2 standard; and
- Automatically shape and compact concrete cubes with minimal error.
Past Challenge Statement
Robotic Cable Pulling in Conduit Systems
Challenge Area
Challenge Statement Owners
Current Situation
Conduit pipes are commonly used to contain electrical and signal cables within buildings. The length of cables used in each project varies widely, ranging from hundreds of metres in smaller residential developments to hundreds of kilometres in larger buildings such as hospitals.
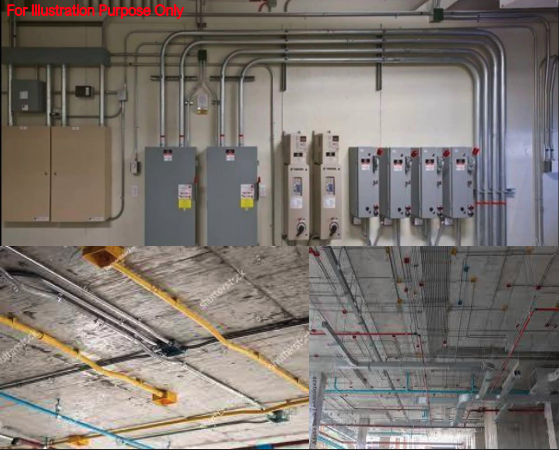
Conduit systems can either be installed as exposed surface-mounted structures or be concealed within concrete. Once the pipes are assembled and the conduit containment system is in place, the electrician will then install the cables. This is usually done by inserting a wire spring into the pipes and pulling it through from the point of entry to the point of exit. Thereafter, a cable is attached to the wire spring, and the electrician will then pull the wire spring in the opposite direction, pulling the cable through the pipes.
However, it is common for wire springs to get stuck at sharp bends and angles, as seen in the diagram below. When such situations cannot be resolved, workers will have to hack into the concrete walls and ceilings to install, maintain, or replace cables, resulting in additional time and resources spent.
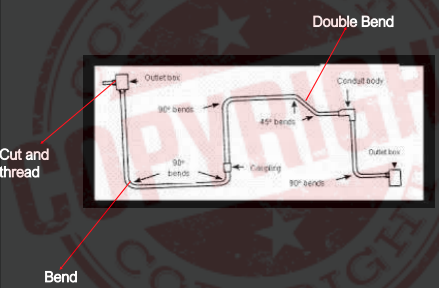
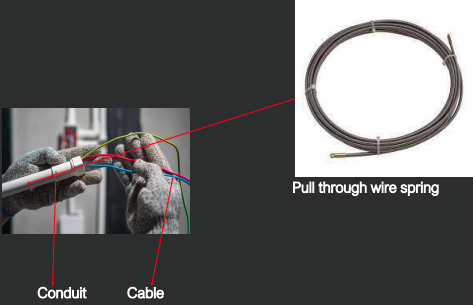
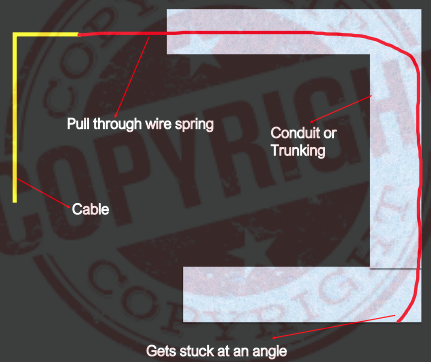
Challenge
DIMeLED is looking for a solution that can automatically thread cables through complex pipes and trunking.
Expected Outcomes
The solution should:
- Be able to pull the pilot cable through existing conduit systems with complex bends; and
- Reduce no of manpower involved in the cable installation process.
Past Challenge Statement
Long-term Monitoring of Deep Foundations
Challenge Area
Challenge Statement Owners
Current Situation
Deep foundations are used in many types of civil infrastructures, such as high-rise buildings, bridges, railway lines, and tunnels. The design and installation of these deep foundations are crucial to ensure that there is sound support and ground stability throughout the lifespan of the structures built above. In Singapore, deep foundations, such as cast in-situ bored piles, are common due to a combination of the type of soil strata and the prevalence of high-rise buildings and other urban infrastructure.
If deep foundations are poorly designed, installed or disturbed by neighbouring works, it may result in settlement, where unequal loading of the foundations causes parts of the structure to become distorted or disrupted. Where settlement is significant, structures can potentially be deemed as unsafe. Extensive and expensive remediation works may then be needed to rectify the issues. In the most severe cases, the structure has to be demolished entirely.
In current practice, a short-term static load test on a small percentage of piles is required to ensure the pile performance conforms with the approved designs. This typically involves a seven-day test on less than 10% of the overall piles installed.
However, this test only provides a snapshot of the expected performance of the deep foundations over a short duration, it does not provide real-time data for the long run. Thus, the responsibility of monitoring and maintaining the performance of a structure built on top of the foundations falls to asset owners and operators, who are required to conduct manual inspections to ensure that the structure is well-maintained and operating safely across its usable lifetime. This manual monitoring technique does not provide data from the root of the cause, providing limited information of the cause of any issues with low resolution.
Recent studies have shown that fibre optic-based sensing can offer accurate, automated, long-term monitoring of deep foundations. Such technology has the potential to provide building owners and operators with critical performance insights of a structure in real-time and high resolution, automating the inspection process and providing information that was previously not attainable. This information would provide firm confidence that assets are operating safely within their design specifications, with data captured from day 1 of the structures installation.
Challenge
Geolutions is looking fora solution capture and provide accurate, automated data, monitoring the performance of deep foundations over the usable lifetime of a building or structure.
Expected Outcomes
The solution should:
- Eliminate the need for manual inspections of foundation piles and hence, reduce manpower;
- Enable automated data capture of deep foundation operating performance over a long period (25+ years);
- Provide reliable and accurate data with resolution down to single digit microstrain in real-time;
- Use a wireless communication protocol that is robust enough for on-site deployment with limited signal loss or data drop;
- Provide a dashboard that allows users online access to updated data; and
- Send alerts to users if measurements exceed the normal range.
Past Challenge Statement
Integrated Automated Reality Capture and Progress Tracking
Challenge Area
Challenge Statement Owners
Current Situation
Progress monitoring in construction sites is a highly manual process. With the large number of stakeholders involved in a project – developers, sub-contractors, suppliers, and engineers – challenges in collecting data and tracking processes not only result in unnecessary delays and costs, but also difficulties tracking errors in works. That can in turn lead to deviations from planned designs.
In greenfield construction, the project design is developed using a Building Information Modelling (BIM) model, which sub-contractors adhere to when carrying out works. While 3D LiDAR scanners can be used to facilitate progress tracking, the post-processing and report generation stage remains a manual process.
For brownfield projects, challenges arise due to missing or inaccurate 2D drawings, especially for older structures. When this happens, engineers resort to multiple site walks to verify equipment and devices on site. While reality capture technology can automate this process, there is currently no way to convert the collected point cloud data into detailed 2D floor plans.
Most commercially available tracking solutions focus on specific tasks or stages in the process, without offering users a seamless experience end-to-end, from data capture to report generation. A fully integrated platform for automated reality capture, data processing, and reporting can streamline project management, save resources, and empower all stakeholders.
Challenge
Exyte Singapore is looking for an integrated, automated, fast, end-to-end system for reality capture and progress tracking in factory constructions sites.
Expected Outcomes
The integrated solution should encompass data capture, point cloud stitching, post-processing, deviation identification, clash prediction, and report generation. The solution should:
- Seamlessly integrate with various scanning robots such as wheeled or legged robot (e.g., Boston Dynamic, AgileX Scout 2.0) ensuring compatibility and adaptability across different robotic platforms.
- Enable robots to autonomously navigate in a factory environment using predefined way-points;
- Enable efficient and accurate automated post-processing of 3D point cloud data obtained from the scans such as auto registration and auto denoising (people removal, temporary works removal if have reference BIM model, outliers noise interference) of point cloud data;
For greenfield projects:
- Calculate deviation differences between planned and actual elements and perform a thorough analysis of variations between planned and actual elements within a BIM mesh and point cloud, ensuring a minimum 5-millimetre precision. Include calculation of variances, incorporate a difference feature for each point, and deliver a comprehensive deviation analysis in a PDF report; and
- Identify potential clashes based on current deviations, considering the original clash-free model, in other words highlighting how deviated as-built elements will impact elements that have yet to be built.
For brownfield projects:
- Automatically generate a 3D BIM model based on the collected point cloud data, with the option to generate 2D floor plans based on this 3D BIM model;
- Automatically identify general components, such as fire extinguishers and other equipment, based on point cloud data; and
- Precisely measure the distances between individual components and represent them accurately on the generated floor plans.
Please download a document (PDF) containing details of detailed requirements of data capture and point cloud stitching, post-processing and deviation identification, clash prediction, and report generation.
Past Challenge Statement
Edge AI Video Analytics for Monitoring Site Safety
Challenge Area
Challenge Statement Owners
Current Situation
Video analytics systems for construction have been quite effective in monitoring site operations for safety, productivity, or security and providing real-time actionable insights for better decision-making.
However, deploying these solutions at construction sites presents significant challenges, primarily stemming from the intricate networking required to transmit CCTV streams reliably and in a cost-effective manner either through 4G/5G, wireless bridges, or mesh networks.
The nature of construction environments, characterised by a limited clear line of sight and numerous metallic objects, severely impedes conventional wireless or wired transmission methods. As a result, ensuring seamless connectivity for real-time monitoring and analysis becomes exceedingly difficult, hindering the efficiency and effectiveness of the Video Analytics systems.
Exyte Singapore is looking for an innovative solution that can significantly diminish the need to set up comprehensive and costly networks across entire project sites, particularly in remote or hard-to-reach areas. They would like to achieve the use of minimal network infrastructure to transmit data from the device to the cloud, to promptly send out notifications and alerts when site safety breaches occur.
Challenge
Exyte Singapore is looking for a solution that can run custom safety video analytics directly at the edge (for example, NVIDIA Jetson), seamlessly integrated with the camera.
Expected Outcomes
The solution should encompass real-time video streaming for remote site oversight, facilitated by a robust command and control system. Furthermore, it must integrate AI-powered analytics directly at the edge device, enabling proactive detection and response to safety breaches.
The solution should:
- Encompass a self-contained unit furnished with essential components, including cameras and supporting infrastructure (for example, poles, waterproof enclosures, and power regulators) for seamless operation.
- Include provisions for cooling the edge devices.
- Seamlessly integrate with any IP camera, regardless of the brand, to facilitate the execution of custom safety video analytics use cases.
- Enable the deployment of custom AI models and safety use cases directly onto the edge AI device.
- On the chosen edge device, demonstrate the ability to process a minimum of 2 camera streams simultaneously in real-time, with each stream supporting at least 3 distinct AI-powered safety monitoring use cases.
- Enable the edge AI functionality to maintain continuous analysis even during periods of low to zero internet connectivity, transmitting alert information once the signal is restored.
- Enable all generated alerts to be accessible on both a mobile platform and a web-based dashboard, providing comprehensive visibility into alert information; and
- Develop APIs to facilitate seamless transmission of alerts to any external third-party system or Exyte's proprietary systems.
Past Challenge Statement
Autonomous Inspection of Roads for Subsidence
Challenge Area
Challenge Statement Owners
Current Situation
Road subsidence and collapse is an issue in large urban cities, due to the intense and large-scale development of underground spaces under which these roads lie. When excavation is carried out to prepare for the installation of new infrastructure, it can result in displacement of the geological structure of the underground spaces. For example, the construction of MRT tunnels can add complexity to the original underground makeup, resulting in a loss of structural integrity. Additionally, rapid urban development results in an increased prevalence of issues like leaks in underground pipes, incomplete backfilling of deep excavation, and rainwater scouring of road structures. As a result, the risk of road subsidence increases.
Furthermore, in large coastal cities like Singapore, geological conditions such as decline in groundwater level and the soil structures can result in instability of foundations, making them vulnerable to traffic loads and other environmental factors. This further raises the risk of road subsidence, necessitating regular monitoring of roads to detect and mitigate road subsidence hazards as early as possible.
Currently, handheld ground-penetrating radar devices are used for inspection, with the aim of detecting areas with high levels of road collapse hazards. However, with so much ground to cover, conducting road inspections manually is an expensive, tedious and time-consuming process. Therefore, Asia Labs sees an opportunity to automate the process of road inspection to ensure that more area can be covered in a significantly shorter amount of time.
Challenge
Asia Laboratories is looking for a solution to automate the process of road inspection with ground-penetrating radar (GPR).
Expected Outcomes
The solution should:
GPR equipment
- Be lightweight enough to be mounted on a small vehicle such as a car or pick-up;
- Be detachable;
- Be multi-band with range of frequency of 50 t0 2000 MHz in order to detect targets ranging from 1cm to 50cm; and
- Have a roadbed detection depth greater than 2.5m and resolution less than 10cm.
- Able to detect the following hidden road defects which include:some text
- Rupture and leakage of underground pipe network;
- Incomplete backfilling of deep excavation;
- Rainwater scouring of road structures;
- Decline in groundwater level; and
- Soft soil foundation structure
Automated radar data interpretation software
- Detect abnormal images picked up by the GPR with at least 90% accuracy;
- Identify infrastructure diseases from abnormal images with at least 80% accuracy;
- Be able to process data at a rate of at least 100 km/day; and
- Have a software interface that is compatible with mainstream hardware devices such as the GPR and other equipment used for the solution.
Past Challenge Statement
Autonomous Inspection of Lift Shafts
Challenge Area
Challenge Statement Owners
Current Situation
The process of installing lifts in a building begins with creating shop drawings based on architectural plans. These typically 2D drawings depict the lift layout through plan and elevation views. Once the building is topped off, EM Services begins the installation process. The lift shaft is usually empty. The lift engineers have limited capability to inspect it until a fixed (scaffold) or moving (example, gondola) working platform is set up.
After the working platform is installed, a "template" indicating guide rail and door sill positions is fixed to the lift shaft's soffit. Plumb lines dropped from this template serve as vertical references for installing guide rails, door headers, and door sills. The lift shaft's verticality is crucial and is later adjusted as needed during installation. Guide rail brackets and sill supports are fabricated based on specific dimensions. Minor adjustments (such as cutting or welding) can be made on-site to accommodate slight variations in verticality.
However, poorly constructed lift shafts with significant verticality issues may require new brackets to be fabricated, resulting in additional cost and delays; some need alterations to the lift shaft, leading to wastage in materials, manpower and time. In some situations, there is no choice but to install a smaller lift than originally planned.
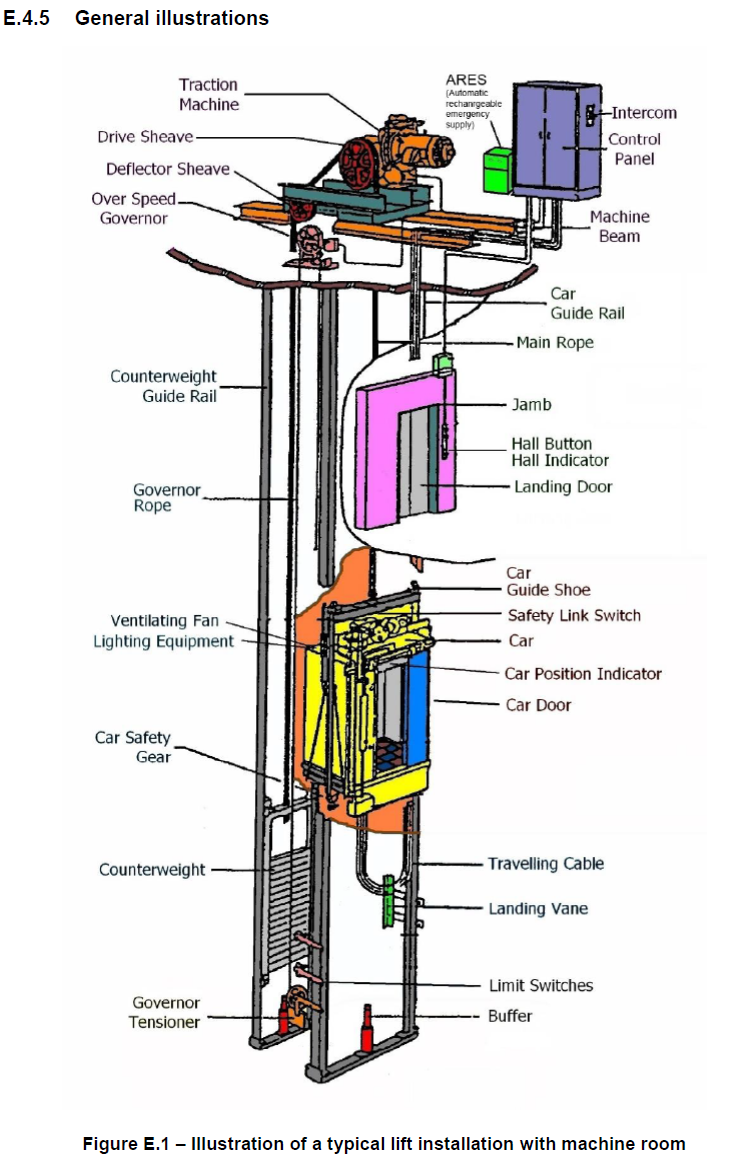
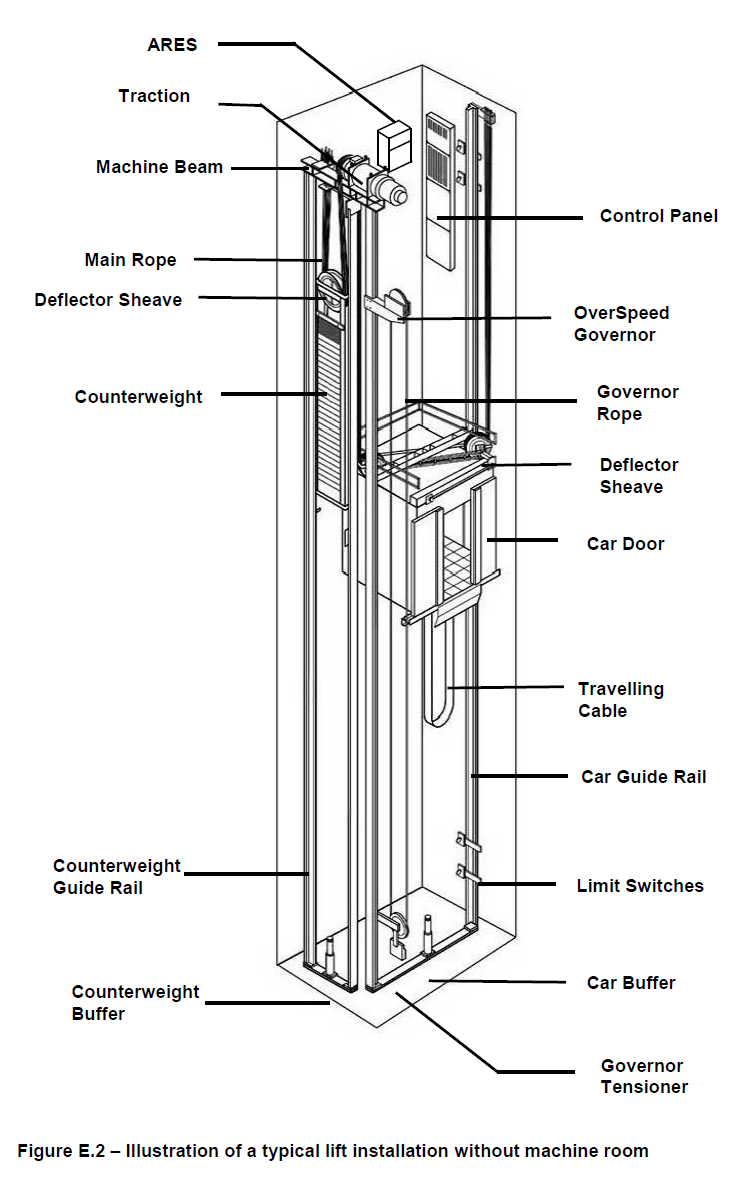
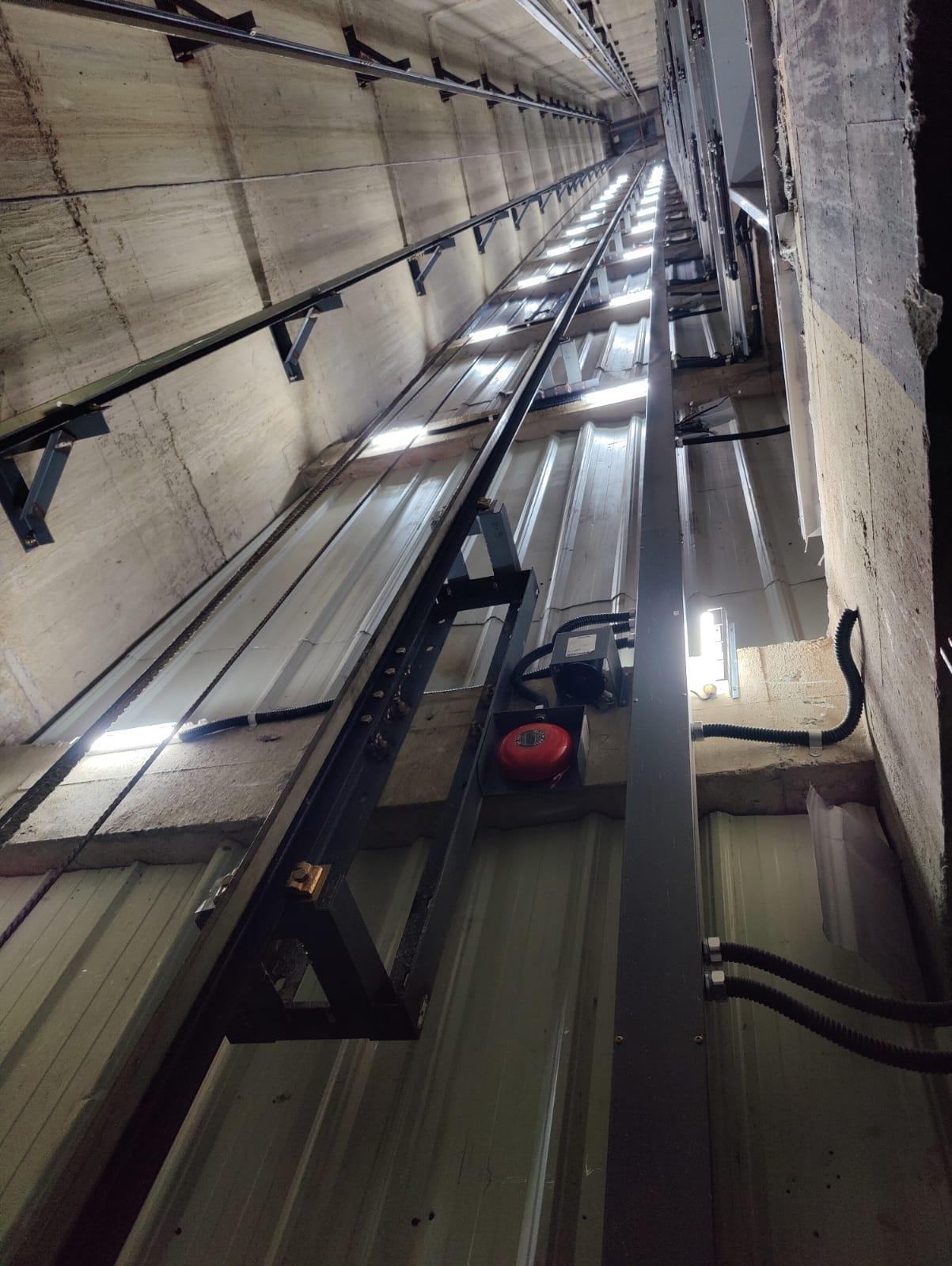
After the lift is installed, a quality assurance check ensures guide rails are vertical, parallel, and within specified tolerances. Any deviations may impact ride quality and cause premature part failure. The inspection is typically performed manually.
While modern construction technology has largely minimised verticality issues in low-rise buildings, challenges persist in high-rise projects (over 50 storeys) and when doing lift replacement works in older buildings. It is also time-consuming to perform annual maintenance inspections on the long lift shafts in these high-rise structures.
Approximately 1,000 lifts are installed each year by all lift companies in Singapore. EM Services is looking into automating these inspection processes, so as to improve the work-at-height safety and reduce the amount of manual labour required to inspect lift shafts for the vertical transportation industry in Singapore. The expected reduction is at least 2 man-days per lift with this automation.
Challenge
EM Services is looking for a solution to automate the inspection of the lift shaft and the lift parts/components installed within the shaft.
Expected Outcomes
The solution should:
- Allow for the dimension and location of the rail brackets to be determined without having to install plumb lines;
- Perform a contactless scan of the entire lift shaft to generate a 3D CAD model with an accuracy of +/- 1mm, allowing for inspection to be done off-site by a Specialist Professional Engineer (SPE);
- Provide 3D video and/or photos with sufficient resolution for offline analysis, in conjunction with the 3D scanning
- Enable the use of BIM for lift installations: with the 3D model of the as-built shaft, the 3D model of the lift assemblies could be fitted into the lift shaft to check for clashes and clearances;
- Map a 50-storey shaft (approximately 150 metres) in 60 minutes or less;
- Supplement the annual mandatory inspection with a scan of the shaft and analyse dimensional variances from earlier scanned models to any changes in the shaft, such as guide rail misalignment; and
- Accumulate a library of detected defects, which can then be used to enhance the auto-detection.
Past Challenge Statement
Autonomous Inspection of HDB Corridors
Challenge Area
Challenge Statement Owners
Current Situation
As the Managing Agent (MA) for various Town Councils in Singapore, EM Services is responsible for carrying out monthly routine inspections of the corridors and stairways for all Housing and Development Board (HDB) blocks under their jurisdiction.
The current practice is for Property Officers (PO) to walk every block, conduct a sweep of each floor, visually identify obstructions, hazards and defects, and record them for follow-up actions. With HDB buildings ranging from 2 to 50 storeys and approximately 600 blocks under a single Town Council, this manual inspection process is very time- and manpower-intensive.
Challenge
EM Services is looking for a robotic solution to automate the inspection for defects and hazards in the common corridors and staircases of HDB blocks, so as to reduce the time and manpower required to conduct these routine inspections.
Expected Outcomes
- Enable real-time connectivity and video streaming to a centralised Command Centre;
- Preferably enable real-time video analytics and identification of defects such as hazards, faulty lights, illegal placement of objects, etc.
The solution should:
- Perform the role of a PO, negating the need for staff to physically be present at the inspection site;
- Be able to forward or backward autonomously in the common corridors, and manoeuvre spaces that are narrower than 1.2 metres in width (Note: While standard HDB common corridors are 1.2 metres wide, residents often place objects such as flower pots and shoe racks in the space);
- Take lifts on its own;
- Be equipped with warning lights and voice annunciations to make its presence known to approaching human beings
- Give way to human beings, and in situations where the robot cannot resolve “right of way” conflicts or becomes stuck due to obstructions, there should be an option to remotely pilot the robot from the Command Centre;
- Operate quietly as it will be deployed between 11pm and 5pm, when there is less human traffic;
- Have a battery life of at least 6 hours;
- Capture images/point cloud data of the corridor and generate a 3D model of the corridor;
- Identify and classify defects, hazards, and obstructions, and pinpoint defect locations on a 3D digital twin of the residential block;
With the increasing deployment of service robots in housing estates, there is an emerging need to manage different robot types and makes, and thus a platform with a common interoperability framework (such as TR93) to manage these robots.
Past Challenge Statement
Autonomous Inspection of Building Façades
Challenge Area
Challenge Statement Owners
Current Situation
Periodic façade inspection (PFI) is mandated by BCA for all buildings older than 20 years and taller than 13 metres. Approximately 30,000 buildings in Singapore are to be inspected every seven years – or around 4,000 buildings a year. This regulation may in future be extended to newer buildings, further increasing the number of buildings that have to undergo routine PFI.
At present, for buildings with mechanically-fixed cladding, there is no way to verify the condition of the cladding framing, bracket, and anchors without manually removing individual panels, particularly for metal cladding, for which scanning methods do not work. This is a time-consuming and costly process.
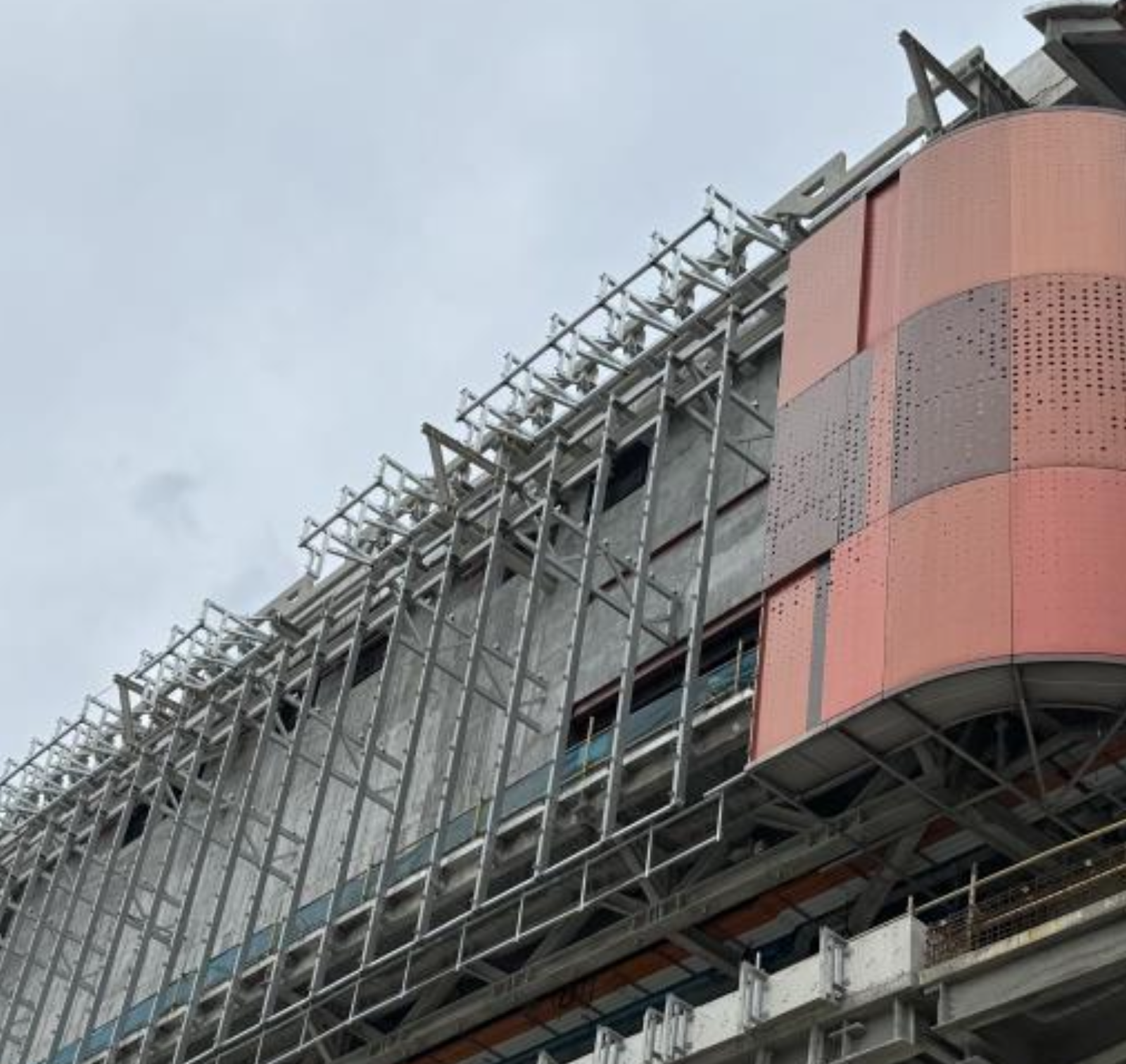
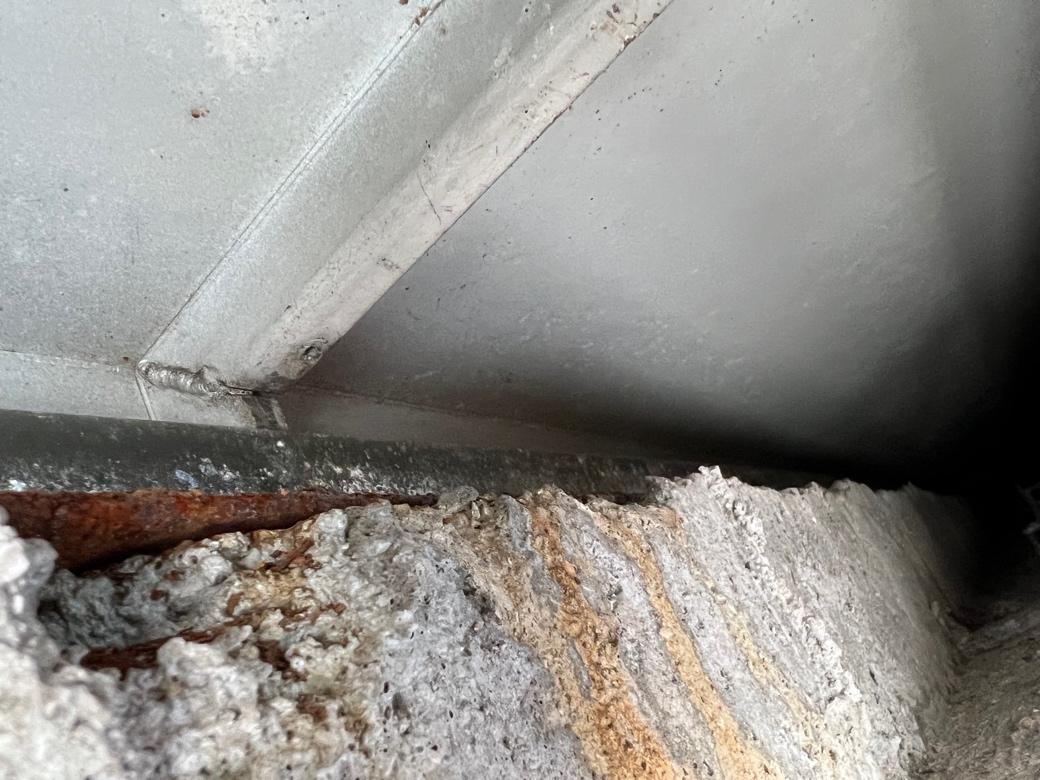
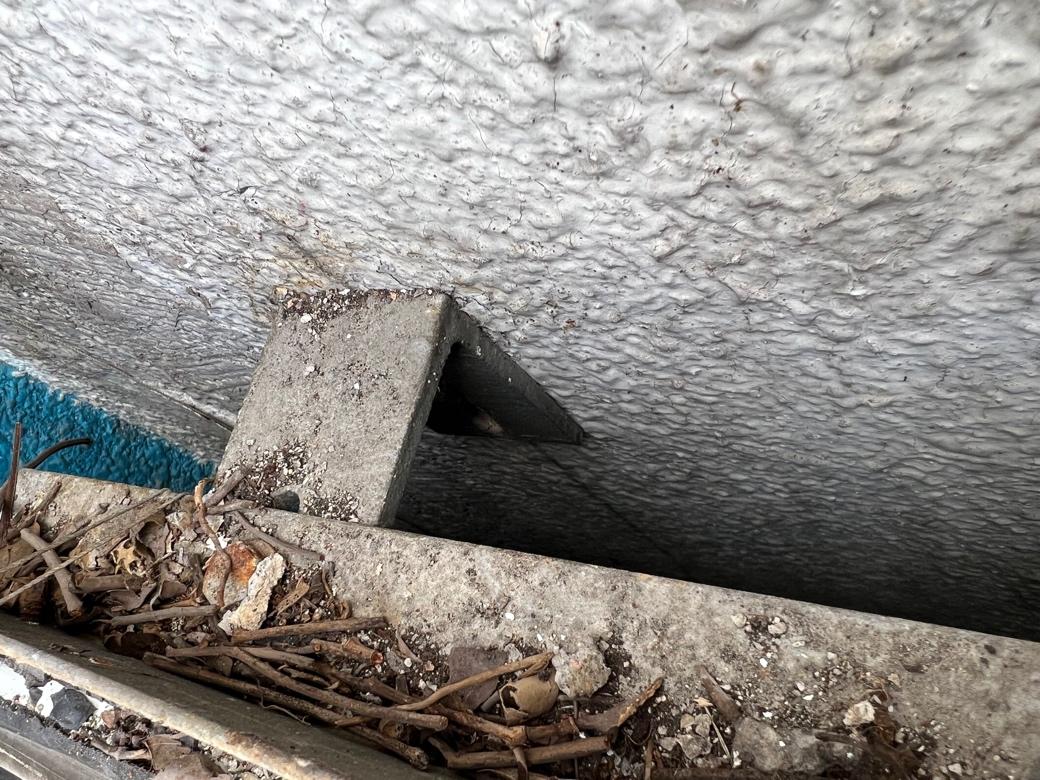
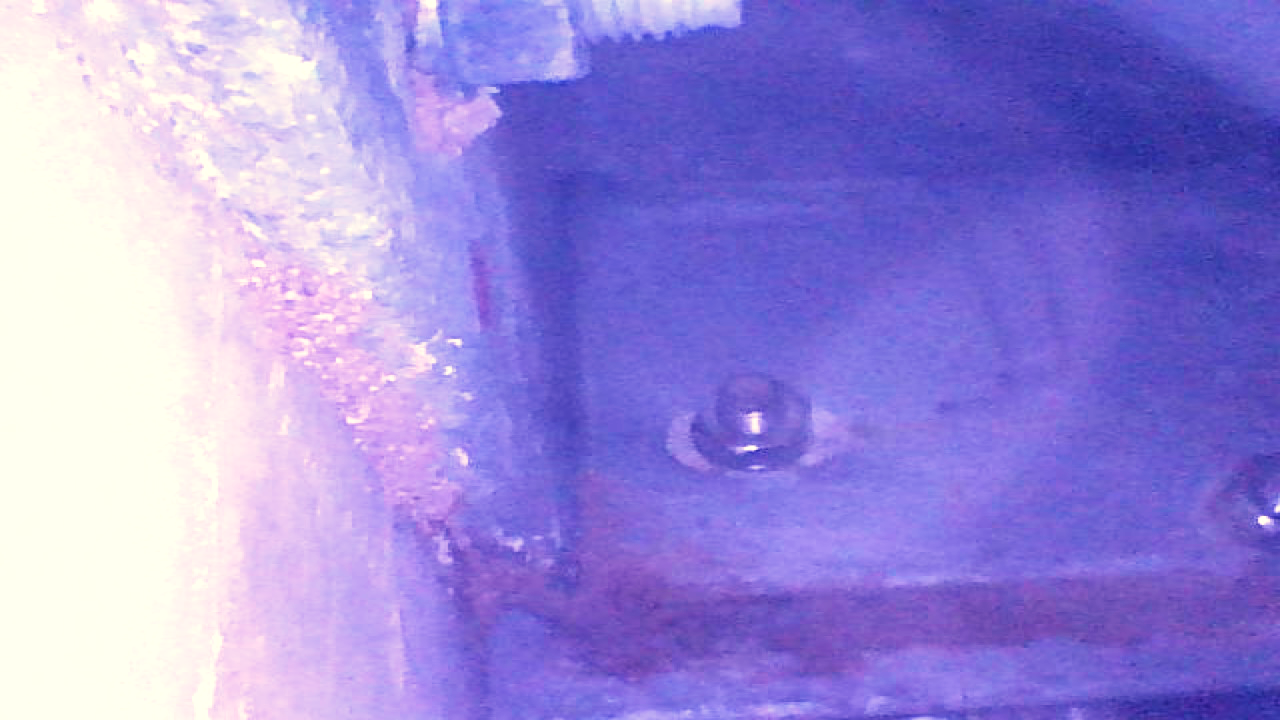
DP Façade is exploring ways to overcome this challenge with PFI with automation – something that would be extremely useful to the hundreds of façade inspectors in Singapore. There is also potential to market the solution to overseas users.
Challenge
DP Façade is looking for a solution to automate façade inspection, one that is capable of visualising the condition of the framing, brackets, and anchors located behind mechanically-fixed cladding.
Expected Outcomes
The solution should:
- Allow a human operator to view a video stream or take photographs to view the condition of the cladding framing, bracket, and anchors, and examine closer for issues;
- Be able to move autonomously or via remote control;
- Be able to move on both horizontal and vertical surfaces;
- Be able to access narrow cladding cavities, which generally range from 50mm to 150mm; and
- Be able to navigate obstacles within the cladding cavity, for example, rainwater down pipes, brackets, runners, lightning protection tapes, etc.
Past Challenge Statement
Automated Tracking of Earthworks and ERSS
Challenge Area
Challenge Statement Owners
Current Situation
The tracking of manpower and equipment productivity, and project progress in construction sites is done manually. The main contractor is required to compile productivity data from their subcontractors and turn them into periodic reports. On top of this being time consuming, the current practice results in missing or unreliable data.
In civil projects, early construction is focused on earthworks and installing the Earth Retaining Stabilising Structure (ERSS). At this stage, utilities, equipment, vehicles, and even CCTVs are often moved around the site. The frequency and extent of such movements makes it challenging to track productivity manually.
Video surveillance systems will become compulsory at all sites with high-risk work activities from June 2025. While most of Penta-Ocean’s worksites already utilise CCTV monitoring prior to this regulation, this new change offers a good opportunity to explore how surveillance data can be leveraged to provide continuous tracking and monitoring of construction activities, thus reducing the need for manual monitoring and reporting whilst. Real-time visibility into productivity, cycle times, and progress, allows for prompt intervention and decision-making. It eliminates the subjectivity and potential errors associated with manual tracking, ensuring more accurate reporting and analysis.
Penta-Ocean has begun trialling video and analytics solutions for use cases such as site safety, equipment identification, and vehicle tracking. For the next stage, they are keen to explore using the video feed to enable new solutions and an integrated system that ingests all data feeds to generate insightful, actionable progress reports.
Challenge
Penta-Ocean is looking for a solution that enables automated, end-to-end tracking and reporting of productivity and progress of earthworks and ERSS at civil worksites.
Expected Outcomes
The solution should:
- Be able to read data from site CCTVs;
- Have 90% accuracy in object and activity detection (see resources for full list of activities to be tracked);
- Be able to detect unexpected downtimes and provide automatically calibrated productivity insights;
- Provide a platform, including a customisable dashboard, that aggregates the site activity data into a dashboard with useful insights
- Enable automated PDF export of regular (option to choose daily, weekly or monthly) progress and productivity reports;
- Be securely hosted with access enabled only by user logins.
Good to have:
- Direction integration with Microsoft Project or Primaverato update percentage-completion progress of each activity;
- Integration with and hosting the dashboard on the common data environment (Fulcrum);
- Enable 3D model visualisation of earthworks progress by photogrammetry;
- Enable BIM model visualisation of piling and D-wall progress, minimally supporting Autodesk Revit and International Foundation Class (IFC)
Past Challenge Statement
Automated Quality Inspections for Building Interiors
Challenge Area
Challenge Statement Owners
Current Situation
CDL’s residential projects are well regarded due to their high quality. This can be attributed to strict and robust quality assurance (QA) and quality control (QC) checks conducted before the handover of each project. These processes are designed in-house, tapping on a wealth of experience and information from past projects to ensure that the execution of the inspections is continually optimised.
Following BCA’s quality mark (QM) inspection, CDL’s quality inspector (QI) and customer service (CS) teams take over the residential units to carry out aesthetic and functional checks, in preparation for the handover to the home owners.
Most projects require inspection of a large number of residential units (600 to 800 units) over a short period (up to three months). The inspections are highly dependent on the speed of preparation by the main contractors. Hence, the time pressure on both the QI and CS teams to conduct their inspections is very high.
The QA/QC inspection process is done visually by CDL inspectors, who then record defects onto a digital platform. However, there is a dwindling number of personnel who have enough experience and knowledge to be effective in doing these inspections, as this workforce ages and younger staff prefer other roles. Therefore, alternative methods of QA/QC inspection will have to be developed.
Challenge
CDL is looking for a solution to automate the interior inspection at residential projects.
Expected Outcomes
The solution should:
- Using a high resolution 360° camera or similar device, detect and identify visual defects that are visible to the naked eye (including, cracks, chips, scratches, stains, peeling paint, rust etc.)
- Accurately identify and categorise at least 70% of the detected defects;
- Complete the inspection of a single residential unit between 10 and 15 minutes (compared to the approximate 45 minutes taken by by 2 human inspectors);
- Be integrated with a digital platform, which can be pre-existing or specially developed to support your solution;
- Automate the process of flattening the images;
- Generate a full defect report for a single residential unit within 48 hours;
- Build up a database of defect images to help train the AI model to achieve higher accuracy; and
- Provide suggestions to optimise the QA/QC inspection process.
Past Challenge Statement
Automated Project Scheduling
Challenge Area
Challenge Statement Owners
Current Situation
When developing a detailed schedule for a new construction project, the planner needs to manually input the details of every task to be performed. A typical construction project involves thousands of tasks, requiring planners to handle and provide large amounts of information, from duration and sequence, to resource type and quantity.
Typically, the planner relies on past productivity figures compiled by their own company as well as their own expertise, to provide estimated figures for each project. Not only is this a very time-consuming and laborious process, it is also prone to errors in judgement that can result in less-than-optimal schedules. For instance:
- Inexperienced planners may not have any past experience to reliably assist them in a new situation;
- The database of productivity figures maintained by the construction company may not be precise, relevant, or sufficiently updated; and
- There is no easy way to gather insights from large databases of past data.
Given the above, planners often find themselves relying on guesswork to produce detailed schedules, resulting in potential productivity losses, hidden costs and risks associated with poor scheduling.
Challenge
Penta-Ocean is looking for a solution that can automate the manual scheduling process and generate accurate, insightful construction project schedules based on past project data.
Expected Outcomes
The solution should:
- Be able to read and edit Oracle Primavera P6 (.xer format) and Microsoft Project (.mpp format) files;
- Be able to handle multiple files from multiple projects (can go up to several hundred .xer and .mpp files) at any one time;
- Collect data on estimated and actual time taken for completion of tasks;
- Maintain an updated database of productivity figures for various projects (see resources for more details);
- Provide insights and recommendations to improve the accuracy of project schedules;
- Input productivity figures to modify new project schedules in .xer and .mpp formats;
- Allow results (productivity range, evolution over time, based on resource number,etc) to be exported in Word and Excel formats;
- Allow users to customise and select categories, items, and task groups for each project (for example, “group by civil, electrical, MEP disciplines” or “group by detailed tasks: rebar installation, formwork installation, finishing”).
Past Challenge Statement
Automated Cost Estimation and Compliance Checks
Challenge Area
Challenge Statement Owners
Current Situation
Despite advances in digitalisation in the built environment sector, many interior design and build projects still rely on manual quantity take-off (QTO) and compliance checks. This process involves many different stakeholders: architects, engineers, quantity surveyors, and consultants. To add to the complexity, there is no standard content or data format amongst them.
As such, data tracking, sharing, verification and approval is time-consuming and prone to errors. This can result in unnecessary delays and impacts throughout the design, tender, construction and handover stages.
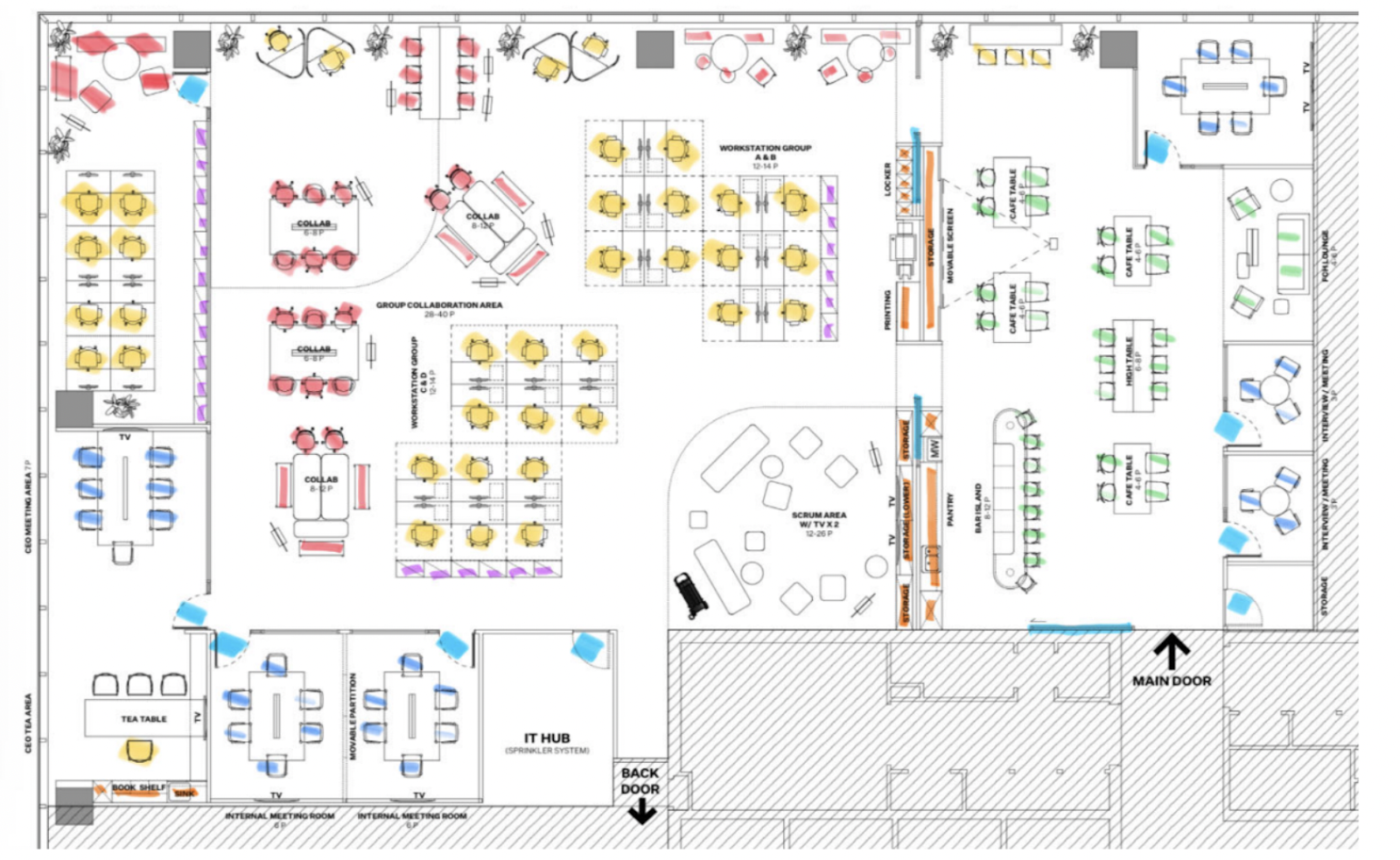
While commercial solutions for automated QTO (such as Togal and Sparkel) are available, they are not designed with Singapore projects and requirements in mind (such as database of commonly used materials, units of measurement, calculation methods) and are thus not as effective in a local context.
M Moser would like to re-invent the way interior spatial data is obtained to dramatically improve efficiency, transforming the traditional process to a truly collaborative and integrative process. AI-based identification and recognition of objects in 2D drawings (for example, DWG and DWF files) and 3D BIM objects (for example, IFC, SketchUp and Revit files) improve the quantification of cost items, cost estimation, and stakeholder coordination process. At the same time, this helps ensure compliance with local requirements.
Challenge
M Moser is looking for a solution to automate the cost estimation tasks and compliance checks, saving over 80% of man-hours compared to the current manual practice.
Expected Outcomes
The solution should:
- Detect and identify at least 80% of typical objects (furniture, walls, doors, and rooms);
- Incorporate a library of objects that is large enough to support the AI applications for QTO and compliance checks throughout design, fabrication, construction, asset delivery, and facility management (AI library development may be phased and prioritised depending on the project development needs);
- Link common open data (e.g. BuildingSMART Institute’s IFC Schema, Singapore’s IFC-SG) and BIM objects with the Building and Construction Authority’s (BCA) Model Content Requirements (MCR) parameters and its project delivery and compliance checks;
- As a start, incorporate IFC-SG schema to auto-classify recognised objects based on VML, with primary information to be attached to individual identified objects and trades;
- Categorise these identified objects with at least 70% accuracy;
- Provide a visual-based platform for various professional disciplines to work with;
- Provide a summary of QTO data in formats tailored to various disciplines, allowing professionals to bypass the data organisation phase (especially for large projects) and proceed directly to data review and adjustment. For example:some text
- Space requirement matching and optimisation for interior designers
- Headcount and occupancy-related computations on fire services/ACMV for engineers
- Budget optimisation and value engineering processes for quantity surveyors
- Enable the data to be viewed on a live visual platform with user-centric UI and UX.
Past Challenge Statement
Automated BIM Database Mapping
Challenge Area
Challenge Statement Owners
Current Situation
Some construction projects require a massive amount of information to be embedded into BIM models. To prepare BIM models which fulfil the level of information required, there are many datasets and essential data attributes (for example, floors, walls, columns, windows, and doors) that need to be tagged to Revit families..
The process of tagging these essential data attributes is done manually, with additional manpower often deployed for this. Tagging is a skilled task that not all staff at consultancy services companies like CPG Consultants, are familiar with, thus presenting a significant operational challenge.
As a start, CPG has set up a centralised data management platform to manage the numerous BIM objects in their database. However, the system in its current form is unable to validate tagged objects in terms of parameter creation, parameter value population, and parameter value checking. Without this validation, it is not possible to determine if the BIM objects meet the requirements for the level of information needed.
Challenge
CPG Consultants is looking for a solution to automate the process of mapping essential data attributes and parameters to their corresponding Revit categories.
Expected Outcomes
The solution should:
- Be able to integrate seamlessly with Revit and other common BIM software where applicable;
- Be able to integrate seamlessly with multiple mapping databases (for example, IFC-SG, MCR, and GWP);
- Enable all Revit families (for example, floors, walls, columns, doors, and windows) to be automatically and accurately tagged with essential data and parameter values from CPG databases;
- Automatically check for the accuracy of parameter values;
- Automatically create system families and classify objects accurately into each family;
- Establish and streamline workflows to tag typical rooms modelled in Revit, including key Revit families (for example, floors, walls, columns, doors, windows, equipment, and furniture). This should apply to other common BIM software where applicable.
Additionally, the solution provider should work towards measuring and quantifying the time savings associated with their solution, in comparison to conventional manual methods.
Past Challenge Statement
3D Digital Twin Model of Building Façade
Challenge Area
Challenge Statement Owners
Current Situation
Undertaking work on building facades can be a challenging task, especially when it comes to coordinating different specialists and the asset owner. It is even more difficult when dealing with buildings that have complex geometry, such as curved facades, recessed areas, and numerous returns. In such cases, a large set of drawings is usually required to document the geometry, making the process even more cumbersome.
Moreover, when undertaking Addition and Alteration (A&A) works, it is crucial for contractors to know where the works are located and potential access restrictions on the building. This can be a time-consuming and complicated process, especially when relying on spreadsheets and written reports.
A 3D digital twin model of the building facade can address these challenges. The client and vendors can access this model to input relevant information, simplifying the process of identifying areas and recording where works have been undertaken. A graphical and 3D representation of the building reduces the need for a large set of drawings with markups for buildings and provides up-to-date observations.
Such a solution also alleviates issues associated with staff changes and offers the potential for further analytics and forecasting. Furthermore, in an A&A tendering process, significant cost savings can result if contractors possess a thorough understanding of building facade issues (supplemented with corresponding images), geometry, and access requirements.
Overall, this streamlines the process of building facade work and improves outcomes for all stakeholders.
Challenge
Arup is looking for a solution that better enables the gathering, presentation and management of building data, particularly of the building facade, so as to improve data organisation and comprehension, auditing, risk management, project management, analytics, and forecasting.
Expected Outcomes
The solution should:
- Create a graphical representation of the building that enables the identification of specific facade elements for observation tagging purposes and facilitates a thorough comparison between the model and the pre-existing structure;
- Effectively distinguish between distinct types of façade elements, such as glazing, cladding, louvres, signages etc.;
- Use recording and retrieval processes, resulting in considerable time savings compared to the traditional method of using 2D drawings;
- Enable real-time monitoring of results and images to ensure transparency;
- Ideally implement a web-based model that is accessible to all vendors, including clients, contractors, engineers, and service providers, through an API, thus ensuring compatibility with various systems and enhancing accessibility for all users;
- Provide a platform for comprehensive tracking of historical data, including replacements, rectifications, window cleaning, BMU servicing, anchor point testing, defects, etc.; and
- Be adaptable to any forthcoming photogrammetry models, enabling the user to toggle them on or off.
Past Challenge Statement
Seamless Material Tracking for Cement Tankers
Challenge Area
Challenge Statement Owners
Current Situation
In a concrete batching plant, it is important to measure the volume of cement that is entering the plant to plan and monitor operations. The conventional way of measuring cement volume is for the cement tanker to drive onto a weighbridge when entering and exiting the plant to calculate the difference in weight and derive the volume. The cement is enclosed in the tanker, so it is not possible to use visual means to determine the volume.
In Singapore, there is limited space within the concrete batching plants to accomodate a large weighbridge that can cater to larger cement tankers. Thus, these plants cannot accept deliveries from larger cement tankers or need to rely on poor estimates.
Challenge
We are interested in solutions that utilise alternative methods to measure the volume of cement carried in a tanker. The solution may be deployed at the entrance and exit of the plant to measure the volume as the tanker drives past.
- The solution must be able to accurately calculate the volume of the cement based on the model or the shape of the tankers. It must be tailored to different models of tankers.
- It must be able to identify the licence plate of the tanker, in order to determine the delivery source.
- It should ideally not require the cement tanker to stop whilst the measurement is being made.
- It could adopt Non-Destructive Testing (NDT) scanners to inspect the content of the tanker to determine the volume of cement. The body of the tanker is typically made out of steel with a thickness of 5mm
- It should not require installation of devices or sensors in or on the cement tanker. This is not practical because Pan-United procures cement from different suppliers.
The solution should include a dashboard that reports on the volume of cement received from the different suppliers. The data in this report will be used to compare with volume indicated in the delivery order (DO).
Expected Outcomes
The solution accurately measures the volume of cement in a tanker to determine the volume in a way that eliminates the use of a weighbridge in a concrete batching plant. It can be for all deliveries by different suppliers.
If this solution is successful, Pan-United is interested to scale it for other materials that are delivered by dump trucks, such as aggregates, and across their 16 plants.
Past Challenge Statement
Routine Inspection of Corridors of HDB Blocks
Challenge Area
Challenge Statement Owners
Current Situation
There are over 10,000 HDB blocks in Singapore. Each town council covers about 600 blocks.
One responsibility of the Managing Agents (MA) of town councils is to perform routine inspections of common areas, such as corridors and stairways, for each block in the Housing and Development Board (HDB) housing estate. This visual inspection is currently conducted by Property Officers (PO) and aims to identify any hazards, defects and obstructions (collectively known as “faults”) that need to be rectified. During the inspection, the PO will survey every floor of the block. Each block has two to 50 floors.
The routine inspection is done once a month for each block, but the frequency can increase based on an as-needed basis.
Challenge
We are interested in robotic solutions that can perform the routine inspection of the HDB corridors and utilise video analytics to identify faults. After the identification of faults, the solution would assist with the investigation by capturing useful information and photographic or videographic evidence, and alert the relevant stakeholders. The list of faults that are of priority to identify can be found under Resources (below).
Here are some of the challenges that need to be addressed before the solution can be deployed successfully:
1) The robot must be able to autonomously navigate the corridors, and not cause damage to private property or not cause harm or disturbance to residents.
- The standard common corridor space has a width of at least 1.2m. However, due to objects placed in the corridors, for example, flower pots and shoe racks, the manoeuvrable space is effectively less than 1.2m.
- The intended deployment time for the robot is 11pm to 5am, when there is little or no human traffic. When it encounters a human, the robot must give the right of way to the human.
2) The robot must be able to call and board the lift to travel between the different floors without human intervention.
- As housing estates have a diversity of lift brands and makes, the robot should ideally be able interface with any lift brand.
- The lift interfacing system should follow TR 93: 2021. It could also refer to the following guidelines : IMDA Guidelines for the Use of Autonomous Mobile Robots for Delivery within Commercial Building
- The lift interfacing system should not involve any modifications to the lift software but could involve attachments to the lift control panels.
3) The robot must be able to navigate between the base station and the destination blocks. It must also be able to travel from block to block to perform routine inspection for up to 4 blocks within one charge cycle.
4) The robot may be required to travel outdoors and be exposed to the elements. The electric and electronics system on the robotics must have protection against rain and water.
5) The robot must be able to be remotely-controlled by a human pilot in the situation that there are errors or challenges faced by the robot during the autonomous operation. It must be able to recognise the errors or challenges, and alert a human staff based at the Command Centre.
- Examples of challenging situations are inability to resolve any “right of way” conflicts, obstructions in inspection pathways, and abusive actions against the robot.
6) It must have real-time connectivity via cellular and channel its video stream to a centralised Command Centre. The video being streamed back from the robot to the Command Centre must be of sufficient quality to allow the video analytics to identify and classify the faults
7) It must not generate noise that can potentially disturb residents.
8) It should have a battery lifespan of at least six hours.
The solution should include a digital interface that supports the programming of the robot’s inspection pathway and monitors the inspection process.
We are interested in the 3D visualisation of identified faults based on their location in the housing estates to further support the operations to manage and rectify the faults. EM Services will work closely with the innovator to generate the 3D map* and inspection pathways of the housing estates required for the autonomous robotic operations.
*BIM data is only available for limited estates.
Expected Outcomes
The robotic solution can autonomously navigate all floors of a HDB block and intelligently identify the faults found in corridors. The solution eliminates the need for Property Officers to perform routine inspections.
Past Challenge Statement
Referencing and Marking for Fabrication of Prefabricated Bathroom Units
Challenge Area
Challenge Statement Owners
Current Situation
Prefabricated Bathroom Unit (PBU) is a bathroom unit that is pre-assembled off-site, complete with finishes, sanitary wares, concealed pipes, conduits, ceiling, and bathroom cabinets, before it is delivered and installed onsite.
At different steps of the fabrication process for PBU, reference lines and markings are required to assist with the accurate installation of concealed pipes, tiles, carpentry and other bathroom fittings. These activities are repetitive and often require additional manpower to help with using measurement, marking or lining tools. Also, the reference lines and markings are done separately by the different trades, and this could result in discrepancies.
Once the installation is complete, the visible reference lines and markings are removed for aesthetic reasons.
Challenge
As the fabrication plant owner, Greyform is interested to lead the streamlining and automation of the process of drawing reference lines and markings. The process could be streamlined into three stages:
- After carcass production – for plumbing
- After waterproofing – for tiling or marble installations
- After tiling and marble installations – for all other trades, such as carpentry and bathroom fittings
We are interested in tools (for example, laser devices), methods, or robotics that can improve the process of producing reference lines and markings. Note that the lines and markings need to be done in stages. We would work closely with innovators to identify and implement the required changes in the fabrication process for the successful deployment of this new tool, method or robotics solution.
The following are some key considerations or specifications:
- The solution must be easy to use for low-skilled workers.
- It must be compatible with Building Information Modelling (BIM) to allow for the extraction of reference data from architectural drawings.
- The resulting reference lines or markings must fall within an accuracy tolerance of ±3mm.
- For the tiling purposes, the solution should be able to produce reference lines at 10mm or less from the corners, depending on the tile thickness.
- The reference line thickness must be less than 2mm, but have good visibility on different surfaces, for example, concrete, tiles, and wood.
- The solution must reduce the total time taken to produce reference lines and markings to less than 30 minutes, including setup and measurement.
- If it produces ink-based lines and markings, the ink must be erasable and not leave any residue stains.
The solution should include a digital interface to carry out simplified programming of the solution based on the PBU to be fabricated.
Expected Outcomes
An innovative tool, method or robotic solution can produce reference lines and markings in less than 30 minutes in total per bathroom unit with minimal human intervention. The solution ultimately saves time and reduces the reliance on human workers, thus, improving the quality and consistency of installations while reducing defects and reworks.
If the solution is proven to be successful, it could be adapted to other offsite fabrication processes.
Past Challenge Statement
Mechanical Splicing of Reinforcement Bars
Challenge Area
Challenge Statement Owners
Current Situation
To splice two reinforcing bars (“rebars”), a coupler is used. Conventional couplers work based on a mechanical principle similar to nuts and bolts: the rebars are screwed into a coupler.
Couplers are difficult to install onsite because the rebars need to be precisely aligned with the coupler during the splicing process. The threads on the rebars and couplers are fine, and thus could be easily damaged during the splicing process.
Challenge
We are interested in alternative designs for the couplers or innovative methods of joining two rebars together.
- The solution must conform to the standards for "Steels for the reinforcement of concrete — Reinforcement couplers for mechanical splices of bar” (SS ISO 15835), especially for the following requirements (more information can be shared upon request to beamp@padang.co) : 1) Tensile strength under static force, 2) Ductility under static force and 3) Slip under static force
- It must eliminate the need to rotate the rebar as part of the installation process, so that less manpower is required.
- It must be applicable to rebars of different thicknesses, ranging from 16 to 50mm.
- It should ideally not require any threading or other types of processing method to be performed on the rebar. This would save at least 10 minutes per rebar.
- It should ideally have a quick installation process of less than 10 seconds per joint.
- The introduction of any additional tools would need to be further considered for important aspects, such as space, safety and skills requirements. The solution should ideally not require any additional tools for the installation process.
- A push-and-lock or a press-and-lock system could be considered.
Expected Outcomes
A new approach to joining two rebars together whilst conforming to SS ISO 15835 standards, the solution would ultimately reduce the manpower required to one person. Also, installation time is reduced from more than 20 minutes to less than 10 seconds per joint.
Past Challenge Statement
Intelligent Remote Monitoring System for Waterproofing
Challenge Area
Challenge Statement Owners
Current Situation
Waterproofing involves the application of waterproof membranes or physical barriers to prevent moisture from penetrating building structures. Waterproofing work is a manual process done by skilled workers. The quality of work is highly dependent on the skill and execution of these workers at each step.
Supervision and timely instructions are important to ensure the quality of work, as the waterproofing project sites could vary in requirements, conditions, and thus complexity. It is time-consuming and costly for the engineers and technical managers to visit the sites, especially those located overseas, to provide supervision and perform quality inspections. Even with site visits, it is still not feasible to monitor and inspect the entire waterproofing process to ensure every step is done with minimal flaws.
Any flaw in the process can lead to waterproofing failures, which then require costly rectification works or worse, cause damage to the building structure or system. Poor workmanship is the main cause of such failures.
Challenge
We are interested in solutions that enable the remote monitoring, inspection and/or instruction of the workers. The solution could even improve the waterproofing process to help the workers consistently achieve good quality of workmanship. It would ultimately help to reduce the need for engineers and technical managers to be onsite to ensure the quality of waterproofing work.
The solution could be IoT devices installed on site, attached to the workers or both, and must fulfil the following requirements:
- It must be easy to set up and not obstruct or interfere with the waterproofing activities.
- It must be able to monitor the activities for the entire surface area that require waterproofing.
- It must work for different waterproofing products. The following products are to be prioritised; their application and installation methods can be found in the respective brochures:
Priority #1 : Traffigard (For Roof)
Priority #2 : Formceal 3000X (For Basement)
Priority #3 : Formdex Uni (For Wet Areas)
- Even with the possibility of 24/7 remote monitoring, the engineers and technical managers cannot dedicate too much of their time to actively monitor the waterproofing process. The solution should enable the entire process to be monitored, but must intelligently alert engineers and technical managers on progress, issues, and abnormalities.
The solution must include a dashboard that integrates the monitoring information and alerts from different project sites.
Expected Outcomes
An imaging device performs real-time remote monitoring of workers performing waterproofing activities, thereby reducing the need for engineers and technical managers to be onsite. The data collected is analysed, and relevant stakeholders are sent alerts regarding the progress, issues, and abnormalities.
Past Challenge Statement
Digital Test of Concrete Strength Development in Precast Production
Challenge Area
Challenge Statement Owners
Current Situation
When carrying out concrete works in a precast plant, especially in an Integrated Construction and Prefabrication Hub (ICPH) where a Just-In-Time (JIT) manufacturing principle is adopted, it is important to ascertain the early-age strength development of the concrete. This is because components can only be demoulded if and when the minimum strength has been attained. This is usually measured using the conventional concrete cube testing method. Additional concrete cubes are also made to be sent to the relevant authorities for later-age strength measurement.
Concrete cube testing is a manual and laborious method. The test also results in a lot of waste as the crushed concrete cubes from the compressive load test will be discarded.
The results from the concrete cube test are often not an accurate representation of the actual state of the precast components due to the differences in curing conditions. Concrete in small cubes has the tendency to gain strength at a slower rate than the precast components that are larger in size. Thus, there are missed opportunities to demould the precast components earlier and have a faster delivery schedule.
Challenge
We are interested in concrete sensing technologies that can measure the real-time strength development of concrete with minimal wastage of materials. Strength development of concrete could be inferred by analysing internal temperature changes of concrete to understand the chemical reactions that have taken place.
A new testing approach could reduce or eliminate the need to carry out the conventional concrete cube testing method. It also boosts production efficiency by giving real-time insights into the concrete structure, so that it can be demoulded as soon as the minimum required strength is attained.
The test will be conducted on flat slabs produced in the ICPH. The solution could be based on different sensing approaches, but need to consider the following requirements:
- The sensing technologies must work for precast elements with thickness of 70 to 90mm. Ideally, the technology can work for thicknesses of up to 150mm.
- Embedded sensors must be small enough to be placed within the rebar structure of the precast components.
- Embedded sensors should ideally operate wirelessly so that there is no additional effort required to find the sensors.
- External sensors must be able to accurately identify the internal conditions, for example, the temperature of the precast element.
- The solution must have a low implementation cost that amounts to <1% of the total component raw cost.
- The solution should consider the concrete strength development benchmarks according to EN206 and other relevant standards set by local authorities.
The solution must include a tablet-friendly digital platform that integrates and visualises the data from the sensors, and produces insights and alerts that can be easily understood by the on-site workers.
Expected Outcomes
The concrete sensing technology accurately measures the real-time strength development of precast flat slabs, so that the demoulding can be done at the best time to increase production by at least 25% and reduce the risk of defects caused by demoulding before the required concrete strength is attained.
Past Challenge Statement
Data-Centric Approach to Trench Cutter Machine Operations
Challenge Area
Challenge Statement Owners
Current Situation
To construct deep base projects and underground structures, a diaphragm wall or a continuous underground wall is used. This method employs Trench Cutter Machines on the ground to excavate a trench along the deep excavation project's peripheral axis while maintaining mud protection.
The Trench Cutter Machine is not easy to operate and relies heavily on the operators’ skill and experience. The operator uses visual observation and monitors the machine’s data to assess the soil condition to determine how best to operate the machine to carry out the excavation.
The diaphragm wall construction method is widely used in Singapore. There are over 60 units of Trench Cutter machines in Singapore, accounting for 40-50% of all machines in the world. However, there is a shortage of experienced machine operators. Poor operations of the machine impact productivity and the quality of the excavation work, and even cause accidents that might delay the construction timeline.
For monitoring purposes, the operators also collect data on the excavation operation and the machine from the control panel, and manually input the data into LT Sambo’s platform.
Challenge
We are interested in solutions that can be retrofitted to the Trench Cutter Machine and can serve to collect and analyse data on excavation operations. The data collected can benefit the construction design process, machine configuration, cost estimation, operator training, and even support future automation of the machine.
We are keen to collect the following data related to the machine and excavation operations. The data will then be channelled to LT Sambo’s platform for recording and site monitoring purposes.
- Time (Y/M/D H:M:S)
- Depth (m)
- Speed (cm/min)
- RPM (rpm)
- Direction (˚)
- Pressure (bar)
- Load (tonne)
- Operator behaviour
- Soil characteristics
Through the processing and analysis of the data, we hope to achieve the following:
- Determine the soil profile of the construction site – Having more accurate records of the soil type and conditions along the depth of the entire trench support more informed decisions regarding construction design, machine configuration, and cost estimation for future projects, especially those located in close proximity.
- Build a knowledge database for training machine operators – Operators can refer to machine operation patterns of skilled operators and learn from them, in order to refine their own performance.
- Lay the foundation for machine automations – The knowledge and data of machine operation patterns can be used to develop machine automations.
The following are the key challenges that the solution need to address:
- It is not feasible to tap into the machine’s control systems, export the data from machines, or develop APIs in the near future.
- The solution should ideally not tap into the machine’s power systems.
Expected Outcomes
An excavation operation monitoring systems collects and analyses data to determine the soil profile and machine operation patterns. The solution ultimately helps to improve productivity and quality of excavation work by supporting decisions to optimise excavation operations, producing insights for the benefit of machine operators, and reducing manual processes.
Past Challenge Statement
Automated Installation of Noise Barrier Panels
Challenge Area
Challenge Statement Owners
Current Situation
Noise barriers are installed along expressways, roads, MRT tracks and construction sites in Singapore to dampen the noise from vehicles, trains and machinery. In order to enable quieter living environments, there are plans to install more noise barriers, for example along the North-South Corridor and along MRT tracks in places like Joo Koon, Bishan and Paya Lebar.
Challenge
We are interested in robotics solutions that can automate the installation of noise barrier panels. The solution should help reduce the manpower and machinery involved in the panel installation process.
The following are requirements and considerations that are important when designing the solution:
- The solution must be able to transport the panels to the point of installation in a manner that does not cause damage to the panels or distort their shape. Each panel has a length of 2m and a height of 0.5m. Its thickness varies between 8mm to 60mm, and depending on type, it weighs up to 12kg.
- The solution must consider how the panels are collected for installation. It could include a panel storage system to ease the collection process.
- It must accurately identify the profile of the column structure and slide the panel to the correct height, depending on which panels have already been installed.
- The panel installation process should take less than 10 minutes per column.
- The solution should ideally be able to automatically move onto the next column once the installation for a column is complete.
- It could be designed to access a height of at least 5m or be integrated with work-at-height equipment, for example, a boom lift.
The solution should include a simple interface to programme and remotely control the robotics solution.
Expected Outcomes
A robotics solution can collect and install noise barrier panels for noise barriers of up to 4.5m in height within 10 minutes. The solution ideally reduces manpower required for this process to just one person.
Past Challenge Statement
Automated Inspection of Precast Components
Challenge Area
Challenge Statement Owners
Current Situation
Quality inspections are required at different stages of the precast fabrication process to ensure that the precast components are constructed accurately according to the required specifications. The inspections are done before the concrete is poured (“pre-pour”) to check the mould, reinforcements, lifting hooks, splice bars, and connectors; and also, after the concrete has hardened (“post-pour”) to check the resulting concrete size, shape and quality, and other items on the checklist (see below).
These inspections are done by Resident Technical Officers or Resident Engineers representing the fabrication plant or consultant. The fabrication process needs to pause for inspection before it can proceed to the next stage. The inspectors need to be present on site to visually inspect the precast components and verify the measurements by taking those measurements with measuring tape and the assistance of other workers. They also need to capture photographic evidence for documentation purposes.
Challenge
Greyform has already adopted robotics to automate the fabrication of various 2D precast components such as wall, column and slab, and is now looking for solutions to automate the quality inspection process.
We are keen to explore the use of advanced imaging and laser-based technologies together with AI to accurately inspect, measure and analyze the precast components to generate the information needed for inspection. The solution must be able to:
- Measure dimensions with a precision of +2mm for panel dimension and +10mm for opening/recess.
- Compare the actual precast components against their Building Information Modelling (BIM) to identify any deviations or defects during post-pour. The comparison is done with the consideration of allowed tolerance for each inspected item.
- Differentiate the rebar mesh from the bottom slab or metal pallet, taking into consideration that the different items can have a similar colour.
The solution should also consider how it can be integrated with Greyform’s Automated Pallet Circulation Plant system.
Expected Outcomes
An AI-based automated inspection system utilizes imaging and/or laser technologies to determine whether precast components are fabricated accurately. For each inspected item, the system produces an inspection report supported by photographic evidence with the measurement (if applicable) and highlights any abnormalities for further action.
The solution reduces the manpower required to support the inspectors by eliminating the need for manual measurement and capturing the inspection data during the fabrication process, so that the process does not need to stop for inspection. In the future, the solution could support remote inspection procedures.
Past Challenge Statement
Automated Floor Tile Grouting
Challenge Area
Challenge Statement Owners
Current Situation
Grouting is the process of filling the gaps in between tiles (ceramic, marble, granite, etc.) for the final finishes of floor and wall. It is a labour-intensive and repetitive process that demands time and skill to achieve the desired finish quality.
Here are the steps involved for the current practice of grouting:
- Mixing of grout material as per the manufacturer recommendation.
- Preparation and cleaning of the area.
- Removal of dirt and unwanted substances from the gap between two tiles.
- Application of grout into the gaps between tiles: the grout is packed into the gap using a plastic card or rubber pad.
- Removal of excess grout and cleaning of tile surface.
Challenge
We are interested in robotics solutions that can automate the entire grouting process for floor tiles in an integrated manner. For a start, prioritise the automation of the steps in the grouting process that have the most potential to generate productivity gain and improvements to quality. Step 4, as described above, is of top priority for automation, followed by Step 5 and Step 1.
The solution for Step 4 should fulfil the following specifications in order to be considered successful:
- It must accurately identify the tile gaps and autonomously navigate a room of up to 20m² to apply grout for at least 50% of the room.
- It must consistently apply grout for different tile arrangements. The tile sizes used in the arrangements could be as small as 150mm in width.
- It must also consistently apply grout to fill the tile gaps of 1 to 2.5mm with different depths (depending on the tile thickness).
- The grout is considered to have been applied consistently when there are no gaps or excess in the application.
- The solution must be able to achieve a recessed joint profile. For a flush joint profile, the robot should achieve as close to what is practically possible.
- It should be able to tailor to different types and composition of grout mixtures and adjust the grout application process accordingly.
- It should be able to apply grout to the corners and sides of the floor tiles that interface with the wall
The robotics solution could take innovative approaches to simultaneously conduct the different steps in the grouting process, instead of a step-by-step procedure taken by human workers. This should reduce the time taken to complete the grouting process and even reduce material wastage (pre-mixed grout is discarded if it hardens). The following solution features are desirable:
- The solution removes excess grout from the gaps and tile surfaces before the grout hardens.
- It is able to carry the different mixture components of grout (for example, cement, water and latex) and mix the grout using a just-in-time approach.
The solution must include a simple digital interface for workers to easily program the robot to perform the grouting works for different projects and monitor the work progress.
Expected Outcomes
A robotics solution autonomously applies grout for a room or area of up to 20m² for floor tiles, which reduces the manpower needed to perform grouting whilst improving the quality of work. The solution would help reduce the duration taken to complete the grouting for one unit by 50%, from 2-3 man-days to 1 man-day.
Past Challenge Statement
Automated Concrete Grinding for Wall and Ceiling Surfaces
Challenge Area
Challenge Statement Owners
Current Situation
Concrete grinding is done to remove the defects on the concrete surface, such as unevenness, bulges and drips, so the quality of the architectural finishes is not affected. Currently, concrete grinding is performed manually by workers using handheld grinders. This operation is not only labour intensive but also poses health and safety hazards to the workers, especially during long periods of grinding work. In order to grind concrete surfaces that are beyond the reach of the worker, for example, walls with heights between 1.5m and 6m, and ceilings, work-at-height equipment is needed. Working at height adds complexity, requires more manpower, and also presents additional safety risks that need to be managed.
Often, the surface finish of grinded concrete surfaces still requires additional treatment, such as skim coating and plastering, before it is ready for a paint finish. As a guide, Concrete Surface Profiles (CSP) were developed by the International Concrete Repair Institute (ICRI) to divide concrete surface treatments into 10 classifications. They are named from CSP 1 to 10 – with CSP 1 being the finest and smoothest surface, and CSP 10 being the roughest and most uneven surface.
For concrete grinding, CSP 1 or CSP 2 is the expected level. Also, the concrete surface should be ready to receive finishes, for example, paint finish, of not more than 10mm.
Challenge
We are interested in robotic solutions that are able to partially automate concrete grinding works as a start and can later be developed into a fully-automated solution. In the early development stages of the solution, the workers can deploy it to do the grinding for a chosen section of the wall or ceiling, and after the work for that section is complete, return to turn on the machine for the next section. This then frees up the workers to perform other activities while eliminating the safety risk associated with grinding.
The current intent is to use the solution to grind the surfaces of a cast in-situ or precast wall that are casted from a typical concrete formwork. The surface profiles of such concrete surfaces are usually even, except for some minor bumps and drips.
The solution should fulfil the following requirements in order for it to considered successful:
- It must accurately grind all of the assigned surfaces to produce a consistent surface quality.
- It must accurately identify the quality and defects of the concrete surface and adapt the grinding accordingly.
- It must be able to perform concrete grinding work on a surface area of no less than 8m2 an hour.
- It must grind surfaces of up to 3m in working height
- It must allow for Interchangeable parts, such as different types of grinding discs and grinding activities.
- The resulting quality of work from the solution must comply with International Concrete Repair Institute’s guide on CSP, where the quality standards for internal and external finishes works shall adhere to CSP 1 to 2, and also to comply with BCA CONQUAS 2019 (Appendix 1, Architectural Finishes, Item 2a - Internal Walls & Appendix 2, External Wall, Item 1 – General Requirements ) as further supplementation.
- The grinding must be performed in full consideration for safety on site and environmental impacts.
- The solution must support the capture of data related to the work done, such as location, duration and errors, for progress tracking and inspection purposes.
- It must be able to operate on site during the construction phase where there are only construction power sources i.e., on-site power generators.
- The solution must be able to fit into material hoists or other equivalent vertical transportation, or work-at-height equipment, with consideration for its size, weight, and portability.
It is also desirable for the solution to meet the following performance specifications:
- It is designed to access heights of up to 6m or to integrate with the common work-at-height equipment for elevation.
- It should ideally improve the quality of works to reduce or eliminate surface treatment works required in order to prepare for the paint finish.
- It should be able to traverse and park on uneven, sloped or stepped areas.
- It should consider how grinding can be done for the following joint areas : 1) joint areas between vertical or horizontal elements (e.g.: slab soffits, wall and floor joints and 2) joint areas between vertical-vertical elements or horizontal-horizontal elements (e.g.: areas between walls and slabs)
Expected Outcomes
The ideal solution can autonomously perform concrete grinding, change grinding parts, and navigate a building floor. For a start, the solution should complete the concrete grinding work on a surface area without human intervention except for deployment, redeployment and termination, and do so accurately and quickly (over 8m2 an hour).
This reduces or eliminates the need for manpower, allows for remote execution and reduces the total cost and time needed to prepare a concrete surface for receiving architectural finish.
Past Challenge Statement
Automated Collection of Carbon Emission Data
Challenge Area
Challenge Statement Owners
Current Situation
Buildings and construction accounts for 39% of global greenhouse gas emissions. Firms in the construction industry, including Obayashi, are increasingly committed to work towards carbon neutrality. As part of Obayashi Sustainability Vision 2050, measures introduced to reduce carbon emissions include:
- Reducing the fuel used by promoting new technologies and labour-saving construction; and
- Developing and practically using energy-saving construction methods and low-fuel consumption and electric construction machinery.
In order to determine the effectiveness of such measures, it is important for Obayashi to first track the current carbon emissions of their sites. Currently, there are no established practices of collecting site-level data related to carbon emissions. If Obayashi were to implement new practices that involve manual data collection, it would be too time-consuming and also produce data that is unreliable due to human factors.
Obayashi wants to reduce both direct and indirect carbon emissions. Indirect carbon emissions are contributed by other companies operating on their sites, such as subcontractors and suppliers
Challenge
We are interested in solutions that can automatically collect site-level data related to carbon emissions. The data of interest include:
- Carbon emissions produced by logistics vehicles, for example, dump trucks and lorries. This can be estimated by determining the number of vehicles operating onsite and their fuel consumption.
- Carbon emissions produced by construction machines, for example, tower cranes and excavators. This can be estimated by determining the number of machines operating onsite, the type of operation, and their energy consumption.
The solution can adopt AI-based visual analytics methods on existing site surveillance systems to collect the data mentioned above for all companies involved without requiring site-wide modifications of vehicles and machines. We are open to adopting new surveillance systems that can support effective and accurate collection of data.
In order to better plan measures and promote collective action by all stakeholders, it is useful if the data collected can generate the following insights:
- Breakdown of the carbon emissions based on company
- Breakdown of the carbon emissions based vehicle or machinery type and model
- Identification of operation abnormalities that could lead to higher emissions, for example, smoke generated from a faulty machine.
The solution can be integrated with project management or logistics management platforms to produce more accurate carbon emissions data on the project sites. It would include a dashboard to visualise the data collected and produce useful breakdown of carbon emissions.
Expected Outcomes
A carbon emission tracking system collects and analyses the emissions data of every vehicle and machine on the whole site regardless of its owner. The data would support decarbonisation measures.
The solution would be part of Obayashi’s effort to develop a carbon emission tracking system that can consolidate and track all their direct and indirect carbon emissions.
Past Challenge Statement
AI-based Video Analytics for Progress Monitoring
Challenge Area
Challenge Statement Owners
Current Situation
Traditionally, progress monitoring of construction projects is often influenced by human factors, as project steps – inspection, recording and interpretation – are done manually by different stakeholders. The resulting reports are often not reliable and require further scrutiny by supervisors and higher-level managers.
Reliable real-time progress monitoring is important to identify issues and potential delays in a timely manner, so that responses like manpower redeployment can be planned and executed to resolve them.
Surveillance tools such as CCTV are being adopted more widely on the construction sites, but these tools have limited usefulness due to the reliance of humans to carry out the remote monitoring.
Challenge
We are interested in AI-based video analytics solutions that can use the footage from existing or new CCTVs to produce useful insights on on-site productivity. Instead of having site personnels to perform frequent checks on the site, the solution would intelligently monitor the site and alert users of any issues or anomalies.
Stage completion and floor cycle are the priority areas for progress and productivity tracking. The tracking of metrics related to manpower, machinery, logistics and material handling are also of interest.
The solution should fulfil the following specifications in order to be considered successful:
- It must integrate with the existing CCTV system. The majority of Tiong Seng’s current projects utilise video surveillance systems from Dahua Technology.
- It must be able to accurately identify and track the following Reinforced Concrete work activities to quantify the stage completion of a floor as the percentage of completion: 1) Reinforcements works, 2)Formwork installation, 3) Concreting works and 4) Formworks removal
- It must be able to compare the actual progress against projected progress based on a seven or ten-day floor cycle time, and identify issues and potential delays.
- It must include methods to boost connectivity to allow for real-time monitoring and analytics.
- The accuracy of the models for the various use cases should be at least 85%.
- It should be able to analyse the duration taken for different stages completed within a floor.
The following are some additional requirements that could further enhance the proposed solution
- The solution could include APIs for interoperability with other enterprise tools and platforms.
- It could be compatible with Building Information Modelling (BIM) to allow for BIM models to be overlaid on real-time CCTV footage or captured images.
- It could involve the installation of new surveillance tools if it can boost the accuracy of the models in a cost-effective manner.
The solution must include a digital platform that analyses the data captured, visualises the data on a dashboard, produces daily progress reports, and alerts key stakeholders on issues and delays. The platform should integrate the existing live CCTV streams through a RTSP setup.
Expected Outcomes
An AI-based video analytics solution can monitor and track structural work as well as formwork progress from the plan view and elevation view of a construction site. The solution allows for early identification of delays and risks that could cause budget overruns.
Past Challenge Statement
Automated Addition and Alteration work plans submission processing
Challenge Area
Challenge Statement Owners
Current Situation
Before renovating a Housing Development Board (HDB) property, the applicant is required to submit the proposed Addition and Alteration (A&A) work plan to HDB to request for approval. The HDB personnel will review the A&A work plan to ensure the works will not affect the building structures before granting approval. This is a tedious and time-consuming process, and involves searching for the relevant building plan drawings specific to the housing project found in HDB�s databases
Challenge
HDB receives more than 2,000 A&A applications monthly. The current workflow to process plan submissions can be streamlined and automated to save significant time for HDB personnel.An intelligent knowledge base could be deployed to automatically execute the task of searching through several databases to retrieve the relevant drawings and then automatically mapped and identified the proposed work in relation to the building structures. The HDB personnel involved can then easily navigate between the relevant drawings in the knowledge base. For example, the HDB personnel is able to access the drawings by clicking on the drawing names found under the �List of Drawings� document, then mapping the submitted A&A work plan against the retrieved drawings from the databases. Concurrently, the process identifies any non-compliances affecting the building structures.The proposed solution should also possess the following features and capabilities:-Ability to recognise and interpret text and image data found in the PDF drawing files;-Provide links to the text and images to access the relevant drawings;-Intelligent system to recognise and map the proposed A&A work plan on different sets of building plans and identify non-compliances.-A user interface that compiles and displays relevant drawings while allowing annotations; and-Ability to generate a supporting report if the proposed A&A work plan submission does not meet the requirements.
Expected Outcomes
The automation solution searches and retrieves relevant drawings from HDB�s databases to support the processing of A&A work plan submissions. The solution streamlines the workflow and saves a significant amount of time and manpower.
Past Challenge Statement
Augmented Reality Visualisation for Precast Element Installation and Inspection
Challenge Area
Challenge Statement Owners
Current Situation
Once precast elements, such as pillars, walls and slabs, have been constructed off-site, they are transported to the site and installed using cranes.The precasters, site supervisors, and engineers currently rely heavily on verbal communication to plan and coordinate the installation, while referencing 3D or 2D drawings. There is still a disconnect between the digital drawings and the realities at the construction site. This could cause misalignment between the stakeholders which leads to incorrect installations and delays in the project.Both installation and inspection of precast elements involve a lot of manual work. The installation team uses simple markings and manual measuring methods to determine the position and orientation of the precast elements before the elements (pillars, walls and slabs) are lifted in. After installation, the inspection process would once again require the tedious process of cross-referencing documents and drawings, and using manual measuring methods to audit the accuracy of the installations.
Challenge
For industrial projects, the number of precast pillars required for installation could amount to thousands. An Augmented Reality (AR) solution that could project the 3D models onto the construction site would help the different stakeholders better visualise the required layout accurate execution of the precast element installation. Once the installation is done, the AR solution can help the inspector to visualise the installation requirements to verify the accuracy. For the initial stage of development, our priority is to have the structural elements visualised. But the solution could further expand to mechanical and electrical systems.The solution needs to be operable from a mobile device or tablet, and could be integrated into the existing Common Data Environment system that is currently used during the inspection process.
Expected Outcomes
The AR solution assists the site stakeholders to visualise and compare the structural installation requirements in 3D. The solution supports better execution of precast element installation.
Past Challenge Statement
Excavator Usage Monitoring
Challenge Area
Challenge Statement Owners
Current Situation
An operator is attached to an excavator throughout his workday. With the help of the foreman and banksman, he gets assigned to tasks that need to be completed with an excavator, and he needs to navigate within the worksite to the specific position to commence work.
Challenge
The utilisation and productivity of the excavators on the construction site could be further optimised with the help of technology to monitor the excavator�s activities. This could support intelligent decision making and better deploy the excavators to their assigned positions at the worksite. Currently, there is limited visibility on the excavator�s activities, and the data needs to be manually collected.In other words, we are interested in monitoring the behaviour of the operator to gain actionable insights on his performance and fitness for work.We seek a sensor and/or IoT system which enables the real-time collection of data that can be analysed and conveyed to the foreman or site manager to support better planning of work activities. Another possible value-adding opportunity is to estimate the total volume of land excavated - data that can in turn be reported to the client.The proposed solution must be adaptable to various models of excavators to increase thechances of deployment of the solution at scale.
Expected Outcomes
The proposed solution augments existing excavators to support monitoring of its operator and its operations (activities). The data gathered from monitoring the excavator and/or the operator is analysed, visualised and reported to the foreman or site manager for review or further action. Ultimately, the solution improves the productivity of the excavators.
Past Challenge Statement
Digital Collection of Production Metrics with Automated Reporting
Challenge Area
Challenge Statement Owners
Current Situation
Production metrics comprise data on the actual quantity of work completed daily, as well as the resources and manpower mobilised for the different trades on a construction site. Currently, site supervisors manually record production metrics on paper. They submit the records to site engineers who compile and tabulate the data collected.This process is tedious, time-consuming and prone to human error. There is also lag time before the generated data is received by the site management and the organisation�s senior management. Hence, these stakeholders do not have up-to-date information on actual versus planned production metrics, to better track the progress of works, investigate on-site issues, and call for early intervention if necessary.
Challenge
A digital solution would assist site supervisors in their daily routine to gather actual production metrics for their site. The existing data collection method is limited by the paper format, and a new digital means would serve to ease the data collection process and allow more data to be collected, such as data specific to individual workers and machinery deployed on-site.The platform must be able to be installed on the personal devices of site supervisors and act as their personal assistant by giving them timely reminders to submit the production metrics. The submitted production metrics would then be sent to the site engineer or management for review and validation.For reporting purposes, the actual production metrics collected would be compiled, tabulated, visualised and compared against the planned production metrics. A solution with the capabilities to calculate the projected days delayed or ahead would also be useful for site resource planning.
Expected Outcomes
The digital solution supports better data collection of the production metrics and automates the process of compiling, tabulating, visualising and comparing production metrics for same-day reporting to site management and senior management. The solution calculates the projected days delayed or ahead to assist with site resource planning. The solution also reduces human errors.
Past Challenge Statement
Common Data Environment System for Construction Management
Challenge Area
Challenge Statement Owners
Current Situation
Construction companies currently use multiple digital platforms to support document management, site management, safety management and project management activities. However, none of the existing digital platforms is able to provide all the features required by these companies.These platforms are not fully compatible with each other, and this results in data silos and even data loss. The data often needs to be retrieved from the different platforms to generate the reports required by various construction stakeholders.
Challenge
We are interested in a Common Data Environment (CDE) system that would comprise a single platform or a consortium of integrated platforms to support document management, site management, safety management and project management activities. The data and information are consolidated and accessible throughout the platform(s).The following are the key features that the platform(s) would ideally have: Document management-Easy access: Allow for access using web and application-based platforms, as well as offline access for sites with low internet connectivity.-Online submission and replies: Allow for online submission and replies of shop drawings, Request For Information (RFI), Submission For Review (SFR), Superintending Officer's Instruction (SOI), and site memos. If a document is pending or overdue for replies, it should be flagged out to the relevant parties. Instruction (SOI), and site memos. If a document is pending or overdue for replies, it should be flagged out to the relevant parties.Site management-Inspection management: Allow for an online and paperless inspection and verification process with an in-built e-signature function.-Defect management: Allow for the creation of defect lists, the automatic channelling of the defect rectification tasks to relevant parties, and the tracking of the completion of rectification tasks.-BIM model viewing: Able to view and comment on BIM models on the platform without the need for a separate authoring software.-Report generation: Able to generate reports using the data from the platform in customisable formats to cater to client or consultant�s requirements.Safety management-Permit-to-work management: Allow for online and paperless application and approval process with an in-built e-signature function.-Safety event management: Allow for online and paperless documentation of safety events, and tracking for corrective actions.Project management-Subcontractor management: Able to track the activities of subcontractors, identify project delays, and estimate the additional manpower required to keep up with the master timeline.-Meeting support: Able to generate useful information to incorporate into meeting agenda and collect meeting minutes.-Progress payment management: Able to accurately track progress for payment claims and help management to visualise the cash flow and the project S-curve. General-Cross-platform support: The CDE system can be operated on portable gadgets such as mobile phones and tablets for site staff�s convenience.-Email integration: Able to integrate with mail service providers, for example Gmail, to extract and send information seamlessly.-Cloud application integration: Able to integrate with cloud applications, such as calendar and cloud storage.-Smart notification: Able to provide timely reminders and status updates.Under Resources, a few bonus features were described by SK E&C with the objective ofenhancing real-time interconnectivity between the BIM models and site activities.
Expected Outcomes
A more comprehensive CDE with most of the features described above that better supports the stakeholders and thus enables them to be more efficient and effective. If multiple platforms are proposed, the platforms must be designed to be fully compatible with each other.
Past Challenge Statement
Personalised Thermal Comfort for Office Occupants
Challenge Area
Challenge Statement Owners
Current Situation
Office spaces, especially those with open concept design, are designed with air conditioning and mechanical ventilation (ACMV) systems that use a blanket approach to regulate the temperature within an area and are not customisable to each occupant�s needs and preferences. The temperature is usually set in the colder range, as it is more widely accepted. This leads to higher energy consumption to meet the cooling demands. Cooling a typical office space is estimated to account for approximately 60% of the total energy consumption of a building. Thus, an effort to reduce cooling demands by 15-20% would significantly save energy and operating costs.
Challenge
We are interested in solutions that can provide personalised thermal comfort for the office occupants, while reducing the total energy consumption of the office. Good thermal comfort allows occupants to improve their productivity at work by creating an environment conducive for their well-being and minimising distractions.The solution should work in tandem or even integrate with the existing ACMV systems in the officeto achieve optimal outcomes. For tenants that lease the office spaces, it is desirable that the solution would require minimal modification of the existing ACMV systems.The following describes how personalised thermal comfort and energy savings could be achieved:-The solution monitors the presence and state of the occupants to understand their thermal comfort requirements.-The solution allows occupants to personalise settings or provide feedback.-The solution can adjust the airflow rate, direction, quality, or moisture levels for the area occupied by an individual.
Expected Outcomes
The solution is scalable office-wide to improve thermal comfort for all occupants at a personal level without sacrificing thermal comfort of their neighbouring occupants. The solution helps companies achieve at least 15% ACMV energy savings in their offices.
Past Challenge Statement
Remote Inspection of PPVC Fabrication Process
Challenge Area
Challenge Statement Owners
Current Situation
The fabrication of Prefabricated Prefinished Volumetric Construction (PPVC) modules is currently done in dedicated production facilities located in Singapore and Malaysia.Quality checks are required during the different stages of the fabrication process to ensure that the PPVC modules are constructed accurately based on the required specifications. The following is a non-exhaustive list of examples of checks required for key elements, which are further illustrated in the document found under Resources:Pre-pour stage-Measure the mould size.-Verify the size of the rebar and measure the spacing distance.-Measure the size of the openings and verify the accuracy of their positions.-Verify the size of the electrical conduit and the accuracy of its position.-Verify the size of the plumbing pipe and the accuracy of its position.Post-pour stage-Measure the resulting carcass size.-Measure the size of the openings and verify the accuracy of their positions.-Verify the accuracy of position for mechanical and electrical provisions.The inspectors currently travel to the site to conduct quality checks on selected activities in the fabrication process. COVID-19 has made it more challenging to conduct these visits. At the fabrication site, the inspectors require the assistance of the workers to make measurements manually using measuring tapes or digital calipers, while they observe and capture photographic evidence for documentation purposes.
Challenge
We are interested in using imaging and/or LIDAR devices enabled by Artificial Intelligence to support the remote monitoring and inspection of the PPVC fabrication process. This potentially allows the inspectors to cut down on their travelling time and generate better documentation. Here are some key considerations: -The current plan is to have imaging devices that can be mounted on the ceilings. But this might offer limited visibility of the fabrication process. We are interested in exploring different ways of deploying imaging devices.-The solution should be capable of accurately measuring the key elements mentioned in the above list of quality checks.-The required precision of the measurement varies according to the inspection task. For rebar size, the measurement needs to be in millimeters.-As part of the inspection process, the solution should capture photographic evidence intelligently and tag the photos for easy reporting.
Expected Outcomes
The solution enables the remote monitoring and inspection of the PPVC fabrication process by intelligently capturing the measurements of the key elements and documenting the inspection process. The solution minimises the need for the inspectors to travel to site to conduct quality checks.
Past Challenge Statement
Close-up Inspection of Building Facades
Challenge Area
Challenge Statement Owners
Current Situation
A facade is an exterior side of a building comprising materials and connections. In response to ageing buildings and increasingly complex facade designs, a Periodic Facade Inspection (PFI) regime will soon be made mandatory to facilitate the early detection of facade deterioration and allow defects to be rectified in a timely manner. Under the PFI regime, the building owner has to engage a Competent Person (CP) to identify areas of problematic facades and carry out full visual and close-up inspection (i.e. involving physical contact with the facade) of the facade condition. As facades can come in different forms (including engineering facades like curtain walls and cladding, and architectural finishes like plaster and tiles), different inspection methods are needed to accurately assess the facades� condition.Cladding FacadesThe use of cladding can be seen on commercial, office and industrial developments. Commonly-used materials for claddings are metal, stone and board materials. The fixings or connections of the cladding to the main structural framing are mostly concealed by the facade barrier.Current methods for the close-up inspection of cladding facade are inefficient and may compromise the safety and performance of the cladding, such as the dismantling and subsequent reinstallation of the cladding panel after inspection and the use of borescopes.Plaster and Wall Tiles Facades Plaster facades are found on almost all Housing Development Board (HDB) housing estates, a majority of private residential buildings, and on several non-residential buildings. Tiles are another type of facade that can be found on older buildings locally.Currently, the close-up inspection of plaster and wall tiles facades involves manual tapping inspection, which is laborious, time consuming and depends largely on the expertise and experience of the inspectors.
Challenge
Inspection technologies, such as mmWave and thermography technologies, could perform the inspection in a non-destructive testing manner and gather information on the surface and underlying defects. For cladding facades, these technologies would eliminate the need to dismantle facade panels or carry out activities that could affect structural integrity.For cladding facades, the following defects are important to be identified:-Dislodgement of panels-Looseness or cracking of the elementsFor plaster and wall tiles facades, the following defects are important to be identified:-Delamination-Debonding-Hollowness-DampnessAdditionally, we are able to omit the usage of height-access equipment, if the inspection technologies and cameras are adapted to a form that can be fitted and integrated into drones, pulley or wall-climbing systems The solution could quickly inspect a large surface to identify areas with a higher risk of failure (such as loose panels) and highlight the risky areas to CP for further investigation.
Expected Outcomes
The solution streamlines the inspection of the building facades, so that a thorough inspection can be done with minimal expense of manpower and time. Ultimately, the solution supports the early detection of facade deterioration, so that the defects are rectified in a timely manner.
Past Challenge Statement
Layout Information Gathering for As-built Services in the Ceiling Space
Challenge Area
Challenge Statement Owners
Current Situation
When carrying out Addition and Alteration (A&A) works to existing buildings, it is important for the contractors to check the actual layout and conditions of the as-built services, such as air conditioning duct, water pipes and electrical trays located in the ceiling space. This information is usually captured in different 2D drawings,and the accuracy of the information needs to be verified on-site as any difference could potentially impact the requirements for A&A works.The conventional method to check the as-built services concealed in the ceiling space requires the following steps:1. Workers use height access equipment that is most suited to the ceiling height. The supervisor or engineer could be present to ensure safety and provide instructions. 2. Workers would open up a hole in the ceiling. The complexity of this task would differ depending on the ceiling type, for example, gypsum ceiling boards and plasterboards.3. Either the worker, supervisor or engineer would visually inspect the ceiling, record the details, and even take pictures for reference. Sometimes, there is a need to climb into the ceiling space for closer inspection.The ceiling would need to be restored to its original condition.Light Detection and Ranging (LiDAR) technology has been tested to improve step 3. However, significant manpower and time are still being exhausted to perform steps 1, 2 and 4.
Challenge
An inspection technology that can capture information on the layout of as-built services with minimal destructive interventions performed to the ceiling would save time and manpower, and improve safety.The following are the requirements for the solution to be useful:-Accurately portray the position and the size of the as-built services;-Capture features (for example, material type) that can help to distinguish between different as-built services;-Identify useful fixtures or fittings (such as valves); and-Complete the scanning and image capturing in an equal or shorter time than theconventional method.The proposed solution should consider how the inspection would be done at height and over a large area with minimal manpower. Any data captured would also need to be organised and referenced to the location.It is also desirable that the information gathered can support the conversion to a Building Information Modeling (BIM) knowledge base.
Expected Outcomes
The solution provides a way to gather details on the layout of as-built services located in the ceiling space while minimising the need to open up the ceiling and disruption to the room occupants. The solution reduces the time needed to check the as-built services and potentially allows the task to be executed with just one person.
Past Challenge Statement
Smart Mechanical RC Pipe Installation System
Challenge Area
Challenge Statement Owners
Current Situation
The conventional method of installing large Reinforced Concrete (RC) pipes with diameters up to 3m and weigh up to 16 metric tonnes involves a crane, lifting equipment, and a team of more than 8 workers with the relevant expertise to execute the work over 6 to 8 hours. The work is manual and poses safety risks, such as lifting equipment failures and pinch points. These RC pipes are installed in open trenches about 6m deep and will become part of the sewer and water infrastructure.To improve productivity, a new mechanical system that uses hydraulics to pull the RC pipes along the sleepers (see picture on the left side) has been developed and has shown successful results of increasing the number of pipes laid per day from 1 to 4. The operating procedure for the mechanical system can be found in the Resources section.
Challenge
The mechanical system could become smarter by incorporating sensors and/or IoT systems. One of the challenges faced is that the system needs to be accurately operated as the pipe reaches its final position to connect with another pipe. If force is overexerted, one or both pipes could be damaged, and would need to be reworked or replaced. The operator currently relies on the banksman to provide accurate information and instructions to act on.We seek a sensor and/or IoT system that can improve the mechanical system or the pipe installation process in at least one of the following ways:-Provide real-time and precise information or alerts on the position of the pipe to the operator;-Simplify or automate the operation of the mechanical system to manoeuvre the pipe into its final position; and/or-Track the performance of the mechanical system and its operation, and analyse the data to improve the entire pipe installation process.
Expected Outcomes
The solution works in tandem with the mechanical system to assist with the RC pipe installation process. The system reduces the total time taken to install an RC pipe by 20% (or one additional pipe installed per day) and decreases the manpower required in the process by at least one person.
Past Challenge Statement
Corrosion Monitoring of Rebars inside Concrete Structures
Challenge Area
Challenge Statement Owners
Current Situation
Corrosion monitoring is important in Singapore due to high humidity levels and proximity to saltwater bodies. Linear Polarisation Resistance and Open Circuit Potential measurements are the common tests for corrosion monitoring of reinforcing bars (�rebars�) inside concrete structures. Both tests require hacking of the concrete cover surrounding the rebars, so that contact can be made with the rebar to complete a circuit. These concrete covers usually have a thickness of 20mm but can have a thickness of up to 50mm for critical structures. Some structures have exposed wires connected to rebars to ease the process of measurement testing, but this cannotbe replicated throughout the entire structure.The current practice is time consuming and hard to execute, especially when workers have limited access to the site (for example, in the scenario where tunnels and the site are already in operation). The hacking of concrete cover damages the concrete structures and could hasten corrosion rates when the rebar is exposed to air and moisture.
Challenge
An inspection or monitoring technology that allows for a non-destructive testing approach towards both the concrete and rebar would improve the corrosion monitoring process by eliminating theneed to hack off the concrete cover. We are open to different measurement techniques, such as impedance or electrical pulse. One way to monitor for corrosion is to study the chlorine penetration and pH level in the concrete layer as well as the condition of the passive film layer surrounding the rebar. Concrete usually has a pH level of 12 and can decrease when chlorine penetrates the concrete and destroys the passive film layer surrounding the rebar. The solution needs to be battery powered and portable to be feasible for field applications.We are also interested in solutions that can help us determine the rate of corrosion and lifespan of a concrete structure.
Expected Outcomes
The solution assists the inspection and/or monitoring process of the state of rebar or concrete to accurately identify if corrosion has taken place. Repair actions can then be taken to prevent further damage. Such a solution would help to eliminate the time and manpower needed to remove the concrete cover, while maintaining or lowering the total cost of corrosion monitoring.
Past Challenge Statement
Integrated Approach to Building Facade Cleaning, Inspection & Repair
Challenge Area
Challenge Statement Owners
Current Situation
The cleaning of industrial/commercial building facades is done annually and in some cases, half-yearly. The work typically involves a minimum of 3 persons, 2 of whom work at height using agondola or rope access system, with one safety personnel. The duration needed to complete the cleaning process of a building typically ranges from one to three months.As part of the process of cleaning, there is further potential for added synergy to also incorporate inspection and repair elements into the gondola or rope access system. Currently, building fa�ades are required to be inspected on a regular basis . Defects are flagged out by the inspectors and prioritised according to severity for follow-up actions. This challenge seeks to primarily develop an autonomous facade cleaning solution, where integration with automated inspection techniques to guide the system to subsequently perform repair works for minor defects would be an added enhanced feature considered.
Challenge
An unmanned robotics solution that can replace current manual methods of cleaning, inspecting and repairing can lead to the following benefits:-Lower the life cycle cost of the building;-Reduce the manpower requirements for facade maintenance;-Improve resilience of the building by detecting and repairing building defects early;-Reduce the safety risk from working-at-height;-Uniform cleaning of building facades to remove human error with results that are highly replicable on other buildings.
Expected Outcomes
The solution must achieve and demonstrate the following outcomes:1. Able to clean facades autonomously.-Solution must be able to clean at least 80% of building facade through roboticmeans;-Able to clean one or more fa�ade types such as reinforced concrete, glass, granite, aluminium etc. Systems that are able to clean more than one facade type or varying fa�ade profiles are preferred;-Able to traverse across most facade features such as window frames and sunshades without intervention2. Reduce cost of operations by 15% or more compared to traditional cleaning methods.3. Reduce dangerous work-at-height and increase productivity at steady state compared to traditional methods of cleaning and inspection.4. Proposals that can inspect and repair fa�ade defects autonomously are a bonus consideration.-Solution must comply with BCA�s Periodic Facade Inspection requirements;-Innovator may propose defect type(s) to be repaired;-Proposal must include proposed method(s) for repair with workable prototype at the end of the project;5. Maintain privacy for tenants whilst work is carried out.Submissions for this challenge statement must also include information such as company/consortium information, method statement, risk assessment and commercialisation plan. Proposed solutions should also be able to sell as independent services (eg. cleaning only) according to customers� needs and solutions that are environmentally friendly (such as reduced water consumption) are a bonus.
Past Challenge Statement
Semi-automated Spot Cleaning of Washrooms
Challenge Area
Challenge Statement Owners
Current Situation
In order to uphold high hygiene standards for the washrooms in commercial buildings, cleaners are assigned to perform scheduled spot cleaning. A cleaner needs to be deployed for per-demand cleaning every time there is feedback that a toilet�s hygiene is unsatisfactory.During the scheduled spot or per-demand cleaning, the cleaner will need to perform the followingactivities:-Cleaning of washroom cubicles especially toilet seats, toilet bowls, and squat toilets-Cleaning of water basins-Damp floor mopping-Clearing of litter on the floor, and emptying rubbish bins and/or-Replacing toilet rolls or refilling soap dispensers as required.There are difficulties in maintaining an affordable human workforce for such tasks.
Challenge
A robotic solution that performs a good portion of the cleaning activities currently being done by human cleaners), could make the cleaning much less labour-intensive. In terms of priority, the robotics solution should minimally be able to clean washroom cubicles based on the followingrequirements:-Cubicle door management, able to push open the door and fit into the cubicles-Toilet seat cleaning, for example use of damp cloth or other equipment to clean the toilet seats and damp mop to clean squat toilets-Seat cover management-Urinal cleaning-Wash basin wiping-Damp mopping-Completing the task within stipulated timingThe washroom environment is dynamic, and the solution considerations are not limited to the above requirements. For a washroom with a floor space of 12 sqm and two cubicles, the solution would ideally be able to finish each washroom cleaning session within 10 - 15 minutes, so there is minimal downtime.For a robotics solution to be feasible for usage in a washroom, it should have the following specifications:-The solution is battery operated.-The solution must not have cameras or collect data that compromise personal privacy.-The solution can navigate within the washroom while the toilet is still open for usage and avoid/stop work when a human is nearby.-The solution must not be hazardous to the human operator and passersby.-Electrical protection (due to damp cleaning)-Manageable weight of machine (due to usage by mature worker strength) if solution transportation of the machine to the washroom-Sleek/slim design of machine to navigate washroom with people inside (due to toilet layout; tight space)We expect the robotics solution would still require human assistance to operate. A cleaner could transport the robot to the start point to commence cleaning, and would inspect the results after cleaning is done.We are open to retrofitting cleaning mechanisms if the solution is capable of cleaning washrooms with high standards, and is cost effective for the initial setup and maintenance.
Expected Outcomes
The robotic solution supports spot cleaning operations by reducing manual labour required and increasing the productivity of the cleaners. The time spent to complete the spot cleaning of one washroom is reduced by 30%.
Past Challenge Statement
Drone Photogrammetry for Site Monitoring
Challenge Area
Challenge Statement Owners
Current Situation
Photogrammetry is a workflow to convert photographs or videos of physical space into a virtual 2D or 3D model that can be measured and manipulated. Drone photogrammetry is already being conducted on a weekly basis for site monitoring.The process to produce drone photogrammetry is time consuming and tedious. It takes several days of flying the drone to capture enough input photos. The flight is semi-automated and still requires a pilot to manage the flight schedule, battery life, and any potential risk to the drone, such as weather.The data processing currently requires a person to download the data from the drone manually and upload it to the photogrammetry software for processing. Any technical issues are hard to resolve due to the lack of local support.
Challenge
Drone photogrammetry is already being done, but the current processes could be further improved. We are interested in a solution that can enhance the drone flight operations and reduce the need for human intervention by intelligently managing the flight schedule, battery life, and risks. It is also desirable if the total flight time can be reduced while maintaining high-quality photogrammetry results. If the data processing can be optimised or automated, the photogrammetry results can be produced more seamlessly and relieve the personnel of theroutine activity.The photogrammetry results would allow site personnel to visualise topographical surveys of the site and compare the results based on the different timestamps. 3D visualisation would be useful to study some key indicators of progress, such as the excavation depth and building height. A web application to display the photogrammetry results is preferred.The challenge statement owner�s own drones are available for use, but the solution provider could propose its own drone if it supports better integration with the proposed solution.
Expected Outcomes
The solution replaces the existing method to produce drone photogrammetry by enhancing the drone flight operation and data processing, while minimising the need for human intervention.
Past Challenge Statement
Delivery of Materials on Building Floors
Challenge Area
Challenge Statement Owners
Current Situation
After the building structure is completed, materials for finishing works need to be carried from theloading points of each floor to the exact location on that floor where the work takes place. Materials, such as bricks, cement, tiles, and wall panels, come in various shapes and sizes, andhave different considerations when being transported.In order to prevent clutter at the worksites, the materials are collected by workers as required before the start of their work. They typically use manual equipment, such as trolleys and wheelbarrows. The planning for the material collection process is done by the supervisor or the workers themselves.At each site, there are different sub-contractors in charge of different tasks, sharing the same loading site.
Challenge
A robotics solution could support the on-demand delivery of materials that are optimised based on the work progress. The solution would allow subcontractors to focus on their tasks at hand and spend less time collecting materials from the loading point.The robotics solution would ideally be able to carry all types of materials, but as a start, bricks and cement are of higher priority. The following technical capabilities and specifications would best fit existing needs:-Capability to navigate the building floor, which includes concrete slab with steps of up to 150mm in height and slopes of up to 1:12 ratio, with minimal human intervention;-Ability to carry loads up to 500kg;-Allowance for the full load of materials to easily fit through a normal-sized door;-Capability to load and unload materials with minimal human intervention;-Prevention of collision with people or structures; and-Manual override of the automated functions.The solution could potentially be further developed to support the planning and management of material delivery for a more seamless experience. Supervisors and workers would be able to track the real-time status of the material delivery, such as information on the collected items and schedule. Data-driven planning would reduce work interruptions due to lack of materials.Such a solution could also help the management of the main contractor and subcontractors to better understand material consumption rates on-site with specific data on material type, time, and location. This would support the replenishing of materials to prevent project delays.
Expected Outcomes
The robotics solution performs on-demand delivery of materials and thus, reduces the manpower required to one (or even none) for each trip to replenish materials for the work sites.The material delivery planning and management features can be integrated into the solution as a bonus to support supervisors and site managers to minimise interruptions and delays in work by providing them with real-time data on materials and the delivery process.
Past Challenge Statement
Unit Layout Plan Optimisation for PPVC Projects
Challenge Area
Challenge Statement Owners
Current Situation
During the design stage of Prefabricated Prefinished Volumetric Construction (PPVC) projects, permutations of unit layout plans are explored manually. Besides fulfilling the architectural vision and requirements, residential unit layout plans seek to maximise the gross floor area and minimise the number of volumetric moulds required.Volumetric moulds are used to produce the concrete finish of constructed modules. The moulds could cost S$70,000-100,000 and take up to three months to fabricate. If the unit layout plan is optimised to allow for more repeated use of volumetric moulds, significant cost savings can be achieved.The following are the steps taken for the design stage of each PPVC project:1. The consultant prepares the unit layout plan and passes it to the PPVC specialist contractor for a design study.2. The PPVC specialist contractor prepares the building information modelling (BIM) drawings, checks the design, determines mould groupings, and submits a study on the mould requirements, which includes details on how the moulds could be used repeatedly.3. The consultant evaluates the mould requirements and revises the unit layout plan to reduce the number of moulds required. The consultant passes the revised plan back to the PPVC specialist contractor to study the mould requirements.The following video provide more details regarding the design stage of PPVC projects:https://youtu.be/kK3yrBd172k
Challenge
The current methods could be replaced with design simulation tools that can automatically generate permutations of the unit layout plans and support the design feasibility study.The unit layout plans generated this way could reduce the number of moulds required while maximising the gross floor area. Based on the plans, the solution would help determine the mould groupings, mould requirements, and the repetitions of each mould.The proposed solution would create a shared environment for both the consultant and contractors to view, discuss and propose design updates.
Expected Outcomes
The solution generates and evaluates the possible permutations of the unit layout plans to optimise the number of moulds and support the design feasibility study. The solution reduces the time and manpower required for the design stage of PPVC by at least 50%.
Past Challenge Statement
3D-Printed Bespoke Building Components
Challenge Area
Challenge Statement Owners
Current Situation
Building designs are constrained by factors such as cost, time and challenges faced during the production process, but never imagination. The benefits of utilising 3D printing in construction provides breakthrough opportunities in various parts of a building such as its facade, allowing for a unique look and therefore potentially increasing the value of the building.Bespoke and complex facades can be made sustainable with 3D printing. It unleashes the potential of fascinating designs while reduces reliance of laborious production processes from the likes of craftsmen.
Challenge
3D printing is recognised as a technology that can enable the sustainable development of bespoke building components. The following should be considered for the solution to be feasible:1. The solution should be able to produce aesthetically pleasing and boundary pushing designs to derive products that include free form and non-symmetrical components.2. The solution must be scalable to cater for larger-scale production of building components.3. The material used for 3D printing must be environmentally sustainable and preferablyrecyclable.4. The solution should be cost-effective, especially if the production is scaled.We are looking for solution provider(s) with the ability to both generate complex designs ofbuilding components using computational methods, and provide the 3D printing technology totheir designs. The solution provider must have strong 3D printing and post-processing capabilities to produce high-quality building components in accordance to its designs. The Challenge Statement Owner will be able to support the solution provider with engineering expertise and insights into the site assembly process.
Expected Outcomes
The 3D design and printing services enable the construction of building components, particularly facades that are aesthetically impressive. As part of the prototyping process, the solution provider will produce computational designs of facades and physical samples (in the range of 300mm x 300mm to 500mm x 500mm) based on the computational design.The solution must cater for large-scale production and consider factors like cost andsustainability.
Past Challenge Statement
Smart Storage, Management and Transportation of Rebar Parts
Challenge Area
Challenge Statement Owners
Current Situation
Constructed modules for Prefabricated Prefinished Volumetric Construction (PPVC) need to be reinforced with metal meshes and reinforcing bars (also known as �rebars�).For this challenge statement, we are focusing on Step 2A of the process to assemble a rebar cage (Identification, collection and sorting of materials required). Currently, the bulk of rebar parts are placed on the storage area floors after delivery by the supplier. The heavy weight of the rebar parts makes it very difficult to implement a rack storage system that could potentially save space.When the rebar parts are needed for assembly, the workers use a custom design trolley (see picture on the above) to collect the required parts and transport them to the assembly site. On the trolley, the rebar parts are sorted on racks for easier retrieval during assembly. However, not all parts are well sorted, and the workers need to re-identify some of the rebar parts through closer inspection and the use of a measuring tape. The (re)identification is not simple, as there is a schedule of 95 rebar parts to choose from, and some parts have similar shapes.
Challenge
A smart storage and management solution for the rebar parts would improve the identification and collection of the rebar parts by the workers. One possible approach is to work with the suppliers to incorporate identification and tracking of the rebar parts as a post-production step in a cost-effective manner.
Expected Outcomes
The solution assists workers to reduce the time required to identify and collect the rebar partsneeded for assembly.
Past Challenge Statement
Computer-aided Interpretation of Drawings for Rebar Cage Assembly
Challenge Area
Challenge Statement Owners
Current Situation
Constructed modules for Prefabricated Prefinished Volumetric Construction (PPVC) need to be reinforced with metal meshes and reinforcing bars (also known as �rebars�). For this challenge statement, we are focusing on Step 1 of the process to assemble a rebar cage (interpretation of drawings by skilled personnel). The drawings of the rebar cages are different for PPVC modules in every project. From the drawing, the skilled personnel deciphers the type and quantity of rebar parts needed for the floor slab and wall rebar cages, and plans how these parts are to be assembled together. You may find in the Resource section examples of the drawings to be interpreted and a schedule of the 95 rebar parts. The skilled personnel then communicates the assembly instructions to the workers.Currently, drawings have been successfully converted to 3D models, and this has reduced the time needed to interpret drawings. However, paper-based drawings are still more practical for the workers on the manufacturing floor.As the interpretation of the rebar cages drawings is done manually, it leaves room for misinterpretation of the drawings that could result in missing rebar parts. If the rebar cages fail the quality checks, the workers would need to amend and rework those cages with errors.
Challenge
The interpretation process could be assisted by the proposed solution to analyse the drawings and/or 3D models, and to provide step-by-step guidance to any workers to determine the required rebar parts and handle the assembly. The solution should be software-based and should support workers by helping them to understand the correct position and assembly sequence for each rebar part.The solution would be highly valuable in the following situations:-When a new module design is introduced in new projects;-When a team of workers are reassigned to accelerate the production of modules that theyare not familiar with; or-When newly-hired workers are being trained for rebar cage assembly.The solution must be able to be used on-site and with portable devices.
Expected Outcomes
The solution reduces the time taken to interpret the rebar drawings, while improving the accuracy of the interpretation, especially during the initial introduction of the drawings.
Past Challenge Statement
Radiation Cooling Solution for External Surfaces of Buildings
Challenge Area
Challenge Statement Owners
Current Situation
In Singapore, cooling is a major driver of electricity consumption and demand. For example, air conditioning consumes a high percentage of energy in buildings.Building owners have been trying to implement passive cooling methods that do not consume additional energy, such as tinting windows with heat- and UV-blocking films, to control heat gain and heat dissipation in a building.
Challenge
For the benefit of environmental sustainability, we are looking for radiative cooling solutions thatcan be applied to the external surface of a building, such as concrete walls, glass facades andwindows. The solution should be most effective during the day, when there are high levels of solarradiation and therefore, greater demand for cooling. Nano-materials are desirable due to their highpotential efficiency.The radiative cooling solution should have the following characteristics:-Radiates infrared waves from solar radiation to outer space and prevent heat gain in buildings;-Can be applied on different surfaces (with concrete, steel and glass in particular); and-Is suitable for tropical climates.
Expected Outcomes
The solution is applied to different surfaces, such as concrete, steel and glass, and reduces heat gain in the building. Importantly, the method used to apply the solution (including the curing process, if needed) must be practical. The cost should also be reasonable.
Past Challenge Statement
Noise Reduction for Residential Units
Challenge Area
Challenge Statement Owners
Current Situation
In a dense country like Singapore, it is common for residential developments to be located near land traffic noise sources, such as major arterial roads, expressways, and MRT tracks. Under the National Environmental Agency�s (NEA) guidelines of land traffic Noise Impact Assessment (NIA), the indoor noise level for new residential developments must not exceed 57dBA (Leq 1 hr) under natural ventilation. Natural ventilation has to be provided by means of one or more openable windows or other openings with an aggregate area of not less than 5% of the floor area of the room or space required to be ventilated.When faced with noise-prone residential developments, developers fulfil the above guidelines in the following ways:-Developers adopt layouts that locate facilities such as car parks on plots closest to noise sources, and residential units far away from the noise sources. -If the above is not feasible, windows or the glass facade are designed to avoid directly facing the noise sources, and windows facing noise sources are double glazed. Developers will also work with acoustic consultants to establish the minimum size of windows that can meet both the noise and ventilation requirements when opened at 30 degrees, in order to be code compliant. -If the above is not sufficient, noise barriers are installed between the transmission path from the noise source to the residential units.The methods above restrict design and could impact the marketability of the development. If the planned mitigation is found to be insufficient during post-construction testing, developers can only resort to erecting noise barriers at the window area. The noise barriers are often not aesthetically pleasing for potential buyers.
Challenge
We are interested in solutions that can be used to reduce the noise from land traffic noise sources. The solution could be installed at windows or openings to absorb, deflect or cancel incoming sound waves, while allowing for natural ventilation. It is important that the solution looks aesthetically pleasing, so that it does not deter potential buyers. It is also important that the solution does not completely obstruct the outside view. If the solution adopts active noise-cancelling technology, it would need to be designed for large-scale integration with the building or compound, and consider long-term sustainability factors, such as power and maintenance requirements.
Expected Outcomes
The solution reduces the noise from land traffic noise sources by at least 10 dBA and below the required indoor noise level of 57 dBA (Leq 1hr), while maintaining good natural ventilation and retaining the marketability of the property. The solution must be suitable for large-scale integration with the building or compound.
Past Challenge Statement
Leveraging on Natural Ventilation to Reduce Energy Consumption
Challenge Area
Challenge Statement Owners
Current Situation
Air-conditioning makes up the largest proportion of energy consumption in most residential buildings. In an effort to induce natural ventilation into buildings and reduce dependency of air- conditioning, wind data is often collected to understand natural ventilation. However, the wind data which is currently available is based on seasonal wind direction with little relation on how surrounding structures could alter the wind speed and direction. A more comprehensive wind data could be collected through on-site logging of wind data though the approach is often time-consuming.
Challenge
Hence, there is a need for a more efficient way to understand natural ventilation in order to maximising its potential to change the design of air-conditioning. In this way, energy efficiency would be increased with reduced dependency of air-conditioning.
Expected Outcomes
The Challenge Statement Owner is seeking an efficient way to collect wind data and eventually develop a �national� wind data model for Singapore. The wind data model shall be maintained and constantly updated to facilitate architects and engineers in shaping their building designs by incorporate natural ventilation as a passive design solution for new buildings
Past Challenge Statement
Maintenance of Commercial Kitchen Exhaust
Challenge Area
Challenge Statement Owners
Current Situation
The lack of maintenance for kitchen exhaust ducts has often resulted in a built-up of discharged greases and fumes around its exhaust filter and ducting. This has compromised the efficiency of the exhaust duct to filer excessive fumes and unpleasant smell from the fumes discharge. The excessive built-up of greases within the exhaust ducts will pose a fire hazard as well.
Challenge
Hence, there is a need for a solution to facilitate maintenance to be carried out promptly and effective to upkeep the efficiency of the kitchen exhaust.
Expected Outcomes
The Challenge Statement Owner is seeking a predictive maintenance solution to improve the maintainability of the kitchen exhaust ducts. The proposed solution shall trigger alerts to the maintenance team to take prompt actions before the aforementioned undesirable outcomes occur.
Past Challenge Statement
Stain-proof Lift Mat for Residential Building
Challenge Area
Challenge Statement Owners
Current Situation
The prevalent usage of Personal Mobility Device (PMD) in Singapore has created a pain point for residential estate town councils in the maintenance of lift mats. The frequent riding of PMD into lifts has resulted in wear and tear leaving behind stubborn stain-marks on the lift mats. With the projected rise in the usage of PMDs, the cost of replacing damaged lift mats is expected to rise too.
Challenge
The existing mat material used in the lifts is unable to withstand the wear and tear due to the frequent riding of PMDs into the lifts, hence, leaving behind stubborn stains and affect the aesthetic of the lift. It is also not cost efficient to replace the lift mats whenever there are such stain-marks.
Expected Outcomes
The Challenge Statement Owner is seeking an innovative material which is elastic and has high durability to sustain the frequent riding of PMDs into lifts. The material shall withstand abrasion due to the riding of the PMD into the lifts. In addition, the new material shall not compromise the aesthetic of the lifts. The new material and its installation shall also not be cost prohibitive to implement in residential buildings.
Past Challenge Statement
Innovative Solution to Deter Bird Perching on Building Façade
Challenge Area
Challenge Statement Owners
Current Situation
Bird perching is a recurring issue faced by residents who live in locations frequent by avian flocks. Besides creating nuisance, birds perching also poses a health hazard to residents. Conventional bird deterrence methods have not been proven effective over time and culling has been used as the last resort when the bird population can no longer be contained.
Challenge
To deter bird perching near residential areas.
Expected Outcomes
The Challenge Statement Owner is seeking a reliable method to deter bird perching near residential areas. The desired outcome of the proposed solution shall meet the following criteria:-It shall not be harmful or affect humans or any other unintended targets in any ways.-It shall ideally solve a recurring bird problem at a location.-It shall not pose any harms to birds.-It shall be cost effective and easy to set up.
Past Challenge Statement
Innovative Cleaning Solution for Residential Buildings
Challenge Area
Challenge Statement Owners
Current Situation
The cleaning sectors in residential buildings has been known to be labour-intensive and less- advanced with the heavy reliance on manual labour and simple cleaning tools such as broom and dustpan. With the projected increase in housing population, increasing the number of cleaners to meet the projected increase in demand of cleaning services is unsustainable.
Challenge
In order to move towards a manpower-lean cleaning sector, the alternative solution is to adopt mechanisation and automation to uplift the operational efficiency and cleaning productivity.
Expected Outcomes
The Challenge Statement Owner is seeking an automated cleaning solution or equivalent that will be able to perform general routine cleaning in common town council estate areas with minimum human intervention. The cleaning solution shall meet the basic requirements to perform thefollowing tasks:-Able to navigate around common areas of a town council estates-Able to be exposed and withstand outdoor conditions-Able To perform general cleaning task
Past Challenge Statement
Improving Indoor and Outdoor Air Quality
Challenge Area
Challenge Statement Owners
Current Situation
The air quality in the outdoor and indoor environment of some overseas cities continues to fall into the unhealthy range and violate the health standard. CapitaLand owns several Business Parks in some of these overseas cities with an average land areas of 50 hectares.
Challenge
The vast land size has posed a difficult challenge to improve and maintain the air quality at a desirable range over a long period of time. Scaling up existing solutions of air purification to improve air quality within and around these premises is not economical and unsustainable.
Expected Outcomes
The Challenge Statement Owner is seeking innovative solutions to absorb pollutants and unhealthy particles e.g. bacteria or virus, to improve both internal and external air quality. Possible approaches could involve measuring and reducing the sources of pollutants to improve and maintain the indoor and outdoor air quality at the desirable range.
Past Challenge Statement
Improving the Effectiveness of Inspection Process and Quality of Works at Pre-cast Yard
Challenge Area
Challenge Statement Owners
Current Situation
Today, pre-casters prepare the moulds for precast concrete components including concrete PPVC modules using their interpretation of hardcopy drawings. Once the moulds are completed, the Resident Technical Officers (RTOs) would conduct visual inspection on the assembled moulds with reference to the drawings. The common items inspected by the RTOs include dimensions of the moulds, reinforcement bar sizes, spacing and lapping length, cast-in-accessories, concrete cover, services openings and cleanliness etc.
Challenge
It is often common for the assembled moulds to fail the quality checks due to inaccuracy of interpretation and human errors. This leads to manpower and time loss in rectifying the non- compliant moulds. Furthermore, RTOs may overlook minor details which results in major rectification especially when the precast concrete components have been installed on site. In addition, precast is done overseas and there are very few or no Resident Engineer (RE) or RTOs who would like to travel to carry out this structural inspection. On top of that, these RE or RTOs have to be stationed full time on-site and the travelling takes too much time and is not productive.
Expected Outcomes
The Challenge Statement Owner is seeking a holistic solution including digital means that is able to improve the productivity and effectiveness of the inspection process as well as the accuracy and quality of works to reduce any manpower and time loss for rectification. Instead of having localized checking inspection, challenge owners are looking for a continuous QA/QC check embedded in the process with the new proposed technology or solution.
Past Challenge Statement
Intelligent Design Prototype Generator
Challenge Area
Challenge Statement Owners
Current Situation
Design options and analysis is time-consuming as it requires an architect to manually research and take into account data such as existing surrounding conditions, weather data or zoning restrictions before coming up conceptual designs.
Challenge
Hence, there is a need to improve design efficiency and productivity through the use of Artificial Intelligence and Machine Learning Capabilities to aid in the process of developing conceptual designs.
Expected Outcomes
The Challenge Statement Owner is looking for a collaborative and innovative platform that combines various datasets (e.g. aerial imagery, environment data and etc.) and project requirements to automatically generate multiple design solutions.The solutions should include these features to aid in the decisions making:-Mass conceptualisation through rapid prototyping-Automated design checks against building code compliance-Automated zoning rrangement
Past Challenge Statement
Intelligent 3D BIM Verification Platform
Challenge Area
Challenge Statement Owners
Current Situation
Current processes of as-built verification is done both visually and manually only covering 5% of the space. Even when a 3D scanner is used to survey 100% of the space, BIM managers/modellers often find themselves spending weeks sitting visually comparing 3D models against 3D scans to detect deviations before updating their as-built models.Hence, such methods are labour-intensive and costly due to time-based survey services costs. In addition, deviations are not detected efficiently as reports usually take weeks to produce.
Challenge
As the industry moves from verification of 2D blueprints to 3D BIM, there is a need for these 3D models to be accurately and progressively verified as part of as-built verification process in order to detect and resolve deviation thus avoiding major reworks. Furthermore, with an up-to-date and accurate 3D BIM (i.e. digital twins) it will ease the handover to between Operation Expenditure (OPEX) to Capital Expenditure (CAPEX).
Expected Outcomes
The Shallenge Statement Owners are looking for a solution to achieve greater Operational Efficiency in their 3D BIM verification process: The proposed solution should be able to: -Increase as-built capture coverage to 100% hence reducing the need for on-site survey.-Utilise Artificial Intelligence to identify dimensional deviations and update 3D models quickly so BIM managers / modellers make timely decisions.-Utilise reality capture hardware tools such as Drones, Photogrammetry technologies and scanners
Past Challenge Statement
Reliable Method of Tagging and Tracking Materials
Challenge Area
Challenge Statement Owners
Current Situation
Materials tagging and tracking in construction projects is a key function that significantly contributes to the success of a project. Construction materials that require tracking include steel bars, pre-cast concrete components and others.
Challenge
This is critical for the pre-casters and site managers as these construction material require proper tracking not just for accountability but also to ensure the quality and reliability of each construction material.Existing solutions such as physical tagging by bar codes or QR codes can be unreliable with challenges such as stickers being damaged, removed or require additional effort to remove after installation.Using exposed Radio Frequency Identification (RFID) tags also will be subjected to similar concerns. But if these tags are embedded, then signal interference caused by concrete and steel reinforcement, as well as the possibility of malfunction of tags losing the identity of the components, give rise to another set of concerns.
Expected Outcomes
The challenge owner is looking for alternatives to existing solutions and welcome further enhancements to current solutions proposals for new innovative solutions with the emphasis on reliability, durability and viability. A dashboard with analytics and notifications to key personnel for the management and tracking of these materials will provide better visibility and efficient progress reporting.
Past Challenge Statement
Automated Quality Control for Prefabricated MEP Modules
Challenge Area
Challenge Statement Owners
Current Situation
Inspection are currently done manually and usually relies heavily on a team of skilled quality assessor to conduct checks on unit. An assessor would have to conduct 2 checks on a single unit:-The first inspection is done when a unit is 50 � 60% complete. This will entail the visual inspection of size, layout, wet works, M&E test.-The second inspection conducted when the unit is complete covers the visual inspection of wall flatness, floor color/firmness, furniture readiness, etc.
Challenge
Therefore, there is a need for a solution to automate and improve the productivity for conducting these inspection while reducing the reliance on manual labour to improve inspection accuracy.
Expected Outcomes
The Challenge Statement Owner is looking for a simple and cost-effective solution to aid in the inspection of units. The proposed solution which could involve the use of Augment Reality or Laser scanning technologies should be able to:-Conduct checks quicker and more accurately as compared to existing methods.-Eliminate the dependence on human judgement during the inspection
Past Challenge Statement
Automated Conversion Between BIM and SDD for MEP Design
Challenge Area
Challenge Statement Owners
Current Situation
The Architect, Engineers and Contractors (AEC) industry has been readily adopting BIM for design and fabrication. During the design stage, the Mechanical, Electrical and Plumbing (MEP) system design is often subject to changes. As there is currently no effective tool to facilitate the update of changes from the original schematic design drawing (SDD) to the BIM design model, there are always discrepancies between both the SDD and BIM design model. This has caused unnecessary challenges during the maintenance of MEP systems.
Challenge
The lack of information links between the SDD and BIM design model has posed a real challenge to design an effective tool to facilitate the synchronising of design changes between both design formats.
Expected Outcomes
The Challenge Statement Owner is seeking for an effective tool in which changes made in the MEP BIM design model could automatically be shared and reflected in the SDD real-time, automatically and accurately. The network of different MEP systems in the final schematic design model shall be generated based on the connections of piping, ducting, cabling segments or other components within the MEP BIM model. Eventually, the developed platform shall provide only one common data source to facilitate an effective maintenance of MEP systems.
Past Challenge Statement
Reliable Method of Tagging and Tracking Materials
Challenge Area
Challenge Statement Owners
Current Situation
Materials tagging and tracking in construction projects is a key function that significantly contributes to the success of a project. Construction materials that require tracking include steel bars, precast concrete components and others.
Challenge
This is critical for the pre-casters and site managers as these construction material require proper tracking not just for accountability but also to ensure the quality and reliability of each construction materials.
Expected Outcomes
Existing solutions such as physical tagging by barcodes or QR codes can be unreliable with challenges such as stickers being damaged, removed or require additional effort to remove after installation. Using exposed Radio Frequency Identification (RFID) tags also will be subjected to similar concerns. But if these tags are embedded, then signal interference caused by concrete and steel reinforcement, as well as the possibility of malfunction of tags losing the identity of the components, giving rise to another set of concerns. The challenge owner is looking for alternatives to existing solutions and welcome further enhancements to current solutions proposals for new innovative solutions with the emphasis on reliability, durability and viability.A dashboard with analytics and notifications to key personnel for the management and trackingof these materials will provide better visibility and efficient progress reporting.
Past Challenge Statement
Knowledge Capture & Data Analysis Platform
Challenge Area
Challenge Statement Owners
Current Situation
A construction project integrates a large amount of processes, making it hard for the Contractor to understand which processes generate value. Each project generates significant amounts of data which are usually collected by the cost control. However, it is often challenging on how these data can be collected and used for improve future projects.
Challenge
There is a need to aid Contractors make better make decisions by providing a holistic view of a construction project based on qualitative, factual element to identify areas to be improved and tasks to be outsourced.
Expected Outcomes
The Challenge Statement Owners are looking for a tool that is able to:-Analyse the processes based on existing data from the cost control and;-Inform the decision-makers about the added-value of a task or a process
Past Challenge Statement
Innovative Solutions to Support Facilities Management
Challenge Area
Challenge Statement Owners
Current Situation
With growing demand on Facilities Management Information developing into BIM Repository, additional processes are being put in place to ensure that consistent information is divulged on labels and facilities before handing them over to project owners.
Challenge
Due to the inconsistency in information between labels and information captured in BIM repository � there is a need for a solution to achieve greater productivity, quality, consistency and maintainability when handing over projects to support subsequent facilities management.
Expected Outcomes
The Challenge Statement Owner is seeking a solution that could help in the handover process.The proposed solution should be able to:-Generate Unify QR labels based on information captured in BIM repository that represent the labels of both Facilities Owner and Contractors & Sub-Contractors. -Allow for real-time validation during the handing over process-Generate label to be tagged on Facilities / Items while link it to the BIM Repository during joint-inspection
Past Challenge Statement
Innovative Predictive Solution for Building Maintenance
Challenge Area
Challenge Statement Owners
Current Situation
Energy consumption accounts for a significant part of the operating cost for commercial buildings. At present there is no holistic way to collect data on the overall health status ofequipment in a building. Existing solutions in the market are too cost prohibitive to be adopted in commercial/non-industrial real estate.
Challenge
There is a need for a cost-effective solution that reduces the reliance on manpower to conduct maintenance check through the use of real-time information to predict building and system failures and break the fragmentation of multi-vendors systems within a building.
Expected Outcomes
The Challenge Statement Owners are seeking for innovative solutions that would be able to:-Gather holistic and relevant building data to enable accurate predictive monitoring (e.g. predict system failure and prescriptive monitoring e.g. algorithms embedded to advise the next course of action / recovery to reduce building disruption and man effort).-Measure a variety of outputs by building equipment (e.g. chillers, HVACs and etc) that have greater risk of failure so as to prescribe timely maintenance / fixes. The solution needs to be able to measure outputs with an analytics tool, prescribing maintenance/fixes with low falsepositive rates to maintain equipment and cost efficiency.-Generate appropriate responses and action plans, suggest various ways to conduct better training and refresher programmes, as well as test and certify readiness of maintenance staff.
Past Challenge Statement
Innovative Location Tracking to Enhance Workplace Safety
Challenge Area
Challenge Statement Owners
Current Situation
It is estimated that 60,000 incidents occur annually within construction sites worldwide. In Singapore alone, workplace injuries rose from 12.4k cases in 2017 to 12.8k cases in 2018 (+2.5%). Amongst them, 41 people died due to fatal injuries. At the same time, according to a research report, large construction projects take 20% longer on average to finish than initial estimates due to poor manpower allocations and/or unforeseen safety issues.
Challenge
In order to enhance construction site safety and productivity, there is a need to provide the project team with clear information such that:-Number of workers that are within a construction site, and which subcontractors they belong to.-The location of the workers to ensure that each individual is accounted for and are within area of work.With these information, it could also allow the benchmarking of the current status with historicaldata to further enhance productivity of further project.
Expected Outcomes
The Challenge Statement Owner is looking for a solution to enhances safety at construction sites through labour location tracking and management of services; while providing geo-fencing capabilities, potential accident notifications and proximity warning systems, through innovations such as AI intervention and incident reports to aid investigations.The solution should also be able to present on a dashboard the workers' locations in divided zones which allows a project team to track workers� indoor & outdoor location and unusual working patterns that might be a potential safety breach.
Past Challenge Statement
Innovative and Intelligent Water Monitoring Tool for Residential Buildings
Challenge Area
Challenge Statement Owners
Current Situation
Water usage accounts for a significant part of operating cost for HDB residential buildings. From time to time, PUB will inform the Town Council of high water consumption experienced in the common areas. Currently there is no holistic data on the water usage in the common areas, coupled with varied reasons on high water consumption. Therefore, it is difficult to pin-point and address the root cause for the high water consumption. Consequently translating to wastages inboth money and precious water resources.
Challenge
Presently, there are no relevant and live system data for building owners/ occupiers to track water consumption in the common areas of HDB residential building. There is only a sole source of data from PUB that could be fragmented at times, making it challenging to predict.
Expected Outcomes
The Challenge Statemet Owner is seeking innovative solutions that will help:-Gather holistic and relevant data of water consumption in the common area of HDB residential building to enable accurate predictive monitoring e.g. predict system failure and prescriptive monitoring e.g. algorithms embedded to advise the next course of action/recovery to reduce man effort and unnecessary wastages of precious water and financial resources.-Measure a variety of tasks that uses water in the common area (e.g. scheduled high pressure block washing, scheduled water tank washing, underground pipe burst) so that any abnormalities in the data could be quickly identified and prescribe timely maintenance / fixes.-The solution needs to be able to measure outputs with an analytics tool, prescribing maintenance/fixes with low false positive rates for cost efficiency. -Aided with a consultant to seek for innovative solutions, such as the use of smart water meterthat complements with an intelligent monitoring system to monitor and manage the water consumption with precision, cost efficient and low manpower effort.
Past Challenge Statement
Holistic Digitisation of Site Environment for Better Site Management and Analysis
Challenge Area
Challenge Statement Owners
Current Situation
Large construction projects take an average of 20% longer to complete than initial estimates due to poor manpower allocations and unforeseen factors owing to the dynamic nature of a construction project. Such delays could have significant impacts to downstream projects.
Challenge
Hence, there is a need for the project team to have a detailed overview of all ongoing activities in real-time that relates to manpower, materials, components, equipment/machinery and vehicles in a construction project to enhance productivity.
Expected Outcomes
The Challenge Statement Owners are seeking for an innovative solution that enables the project team to identify areas of bottlenecks in a project which could include site logistics, handling of component and construction cycle activities. The solution should enable the project team to track location and working pattern through a dashboard that divides the site into zones, giving an overview of activities in each zone.
Past Challenge Statement
Digital Twin for ICPH Facilities Management
Challenge Area
Challenge Statement Owners
Current Situation
Within an Integrated Construction Prefabrication Hub (ICPH), there are various equipment and machinery that needs to be maintained. Current processes of maintaining this equipment arereactive and the maintenance process commences only after a fault is detected. Creation of a digital twin for the ICPH can allow paperless transactions and increase efficiency.
Challenge
The use of paper records is unreliable and inefficient for the facilities management. Further this does not provide real-time data of equipment performance allowing for predictive maintenance
Expected Outcomes
A dynamic virtual representation of the physical assets in the ICPH or a digital twin. Through Artificial Intelligence (AI) and Machine Learning (ML), the digital twin shall make use of real- time data from IoT sensors to virtually detect the performance of equipment, how it is operating, and when it may require maintenance. It shall potentially enable remote operation and troubleshooting, reduce energy and water wastage, enable examination of the causes of past issuesor breakdowns, and, lastly, provide opportunities to predict future performance or failures to support preventative maintenance.
Past Challenge Statement
Innovative Hoisting Mechanism to Enhance Lifting Safety
Challenge Area
Challenge Statement Owners
Current Situation
Precast modules are usually lifted by wires with the safety of the lifting process very much dependent on the experience of the crane operator. Further, existing operations does not take intoaccount factors such as; unbalanced loading caused by uneven distribution of stresses across chain pulleys or non- visible damages to cable ropes due to wear and tear.Hence, any unintended / accidental release of these precast modules during lifting operation would compromise the safety of the lifting equipment, operator and construction crew.
Challenge
It is essential to enable the crane operator to make better decisions when lifting precast modules for installation thereby making the lifting process safer.
Expected Outcomes
The Challenge Statement Owner is seeking for a solution that enables the crane operator to make adjustments based data collected when lifting precast panels. These data should include factors such as; the distribution of weight when lifting precast modules and stress distribution across the lifting beam.The proposed solution could involve the use of sensors integrated to the lifting equipment to provide feedback to the crane operator in the crane cabin in real-time. This feedback could also trigger alarms to both the operator and ground crews while restricting further operations when thresholds are breached.
Past Challenge Statement
Determining Integrity and Durability of Existing Buildings and Aging Structures
Challenge Area
Challenge Statement Owners
Current Situation
Due to the nature of environment and the usage of buildings, existing solutions are unable to accurately determine the condition or reliability of the materials such as steel, reinforced concrete (RC) for the beams, columns and other essential structures that affect structural integrity of a building. Inspection is usually done by a PE (Professional Engineer) through visual inspection periodically, usually in a range of 5 years. Many challenges arise in determining a building structural integrity, one of them is the lack of physical access or unseen parts of the area or structure. Inspection is often limited to visual inspection of accessible areas.
Challenge
Currently, there are a few existing methods in the market that require sensors to be embedded into the structure but this causes other issues such as sensor data reliability and cost effectiveness for sensors to be embedded into all structure.
Expected Outcomes
Challenge owners are looking for a solution to improve and simplify the inspection process and provide reliable measurable data that is low cost and can be implemented on existing buildings. These data can be in the form of and not limited to yield strength, corrosion of reinforcement, strain, crack width and etc. Early indications can help determine if building should be decommissioned or strengthened or rectified to ensure overall safety.
Past Challenge Statement
Smart Measuring System for Aggregate
Challenge Area
Challenge Statement Owners
Current Situation
In order to determine the volume of aggregates stocks, vehicles loaded with aggregates stocks have to be weighted twice, before and after unloading of the aggregate stocks at the unloading bay. Since the weighing platform and unloading bay may not be located next to one another, vehicles have to spend unnecessary time travelling between the weighing platform and unloading bay. In addition, the measurement results are not updated real-time and are often prone to human errors.
Challenge
Hence, despite the effort to minimise disruptions caused administratively, the process of keeping track of these daily aggregate stock is still tedious and time-consuming due to the constant inflow and outflow of these aggregates.Therefore, there is a need for a more productive measuring solution which is able to provide real-time and accurate results for the measurement of the aggregate stocks volume.
Expected Outcomes
The Challenge Statement Owner is looking an economical and efficient solution to measure the volume of aggregate stock. The proposed solution should: -Receive aggregate images and convert it into a 3D model-Calculate the volume of aggregates based on the 3D model and estimate the tonnage of the aggregatesSeamless sharing of information between front end and back end offices
Past Challenge Statement
Smart Assembly of Rebar Cages
Challenge Area
Challenge Statement Owners
Current Situation
For Prefabricated Prefinished Volumetric Construction (PPVC), modules need to be reinforced with mesh and reinforcing bars (also known as rebars).The steps involved in fabrication and the assembly free-standing volumetric modules are:Step 1: Interpretation of rebar drawings by skilled personnelStep 2: Assembling the mesh and rebar to form a structured cageStep 3: Install the rebar cage into the mouldStep 4: Closing of steel mould and installing of services ductsStep 5: Checking and closing of mouldThe steps require the effort by a 4-man team that takes 8 � 10 hours a day to prepare the rebar cages.
Challenge
It is extremely time consuming process to assemble rebar cages. Moreover, as the interpretation of the rebar drawings are conducted by human, it leaves room for misinterpretation of drawings could result in missing rebars and links.If the checks fail (often due to the inaccuracy of rebar drawing interpretation), workers have to amend and rework these the cage from scratch. This means more time required to amend the rebar cage.
Expected Outcomes
The Challenge Statement Owner is seeking innovative solutions to save time and manpower in the fabrication and assembly of rebars. The proposed solution should also boost the accuracy of the rebar cages� structural integrity and greatly reduce unnecessary re-work and save time and manpower in reading/interpretation, fabrication and assembly of rebars.
Past Challenge Statement
Enhancing the Accuracy and Productivity of Corrosion Monitoring
Challenge Area
Challenge Statement Owners
Current Situation
Monitoring of the corrosion status of reinforcement bar are estimated from open circuit potential measurement and linear polarisation resistance. Both these tests are intrusive as they require hacking off the concrete cover of the reinforcement bars before reinstating them each time. Alternatively, corrosion status could also be estimated by embedding connection wires and leaving them exposed for the continuous measurement.
Challenge
Such methods of monitoring of corrosion status are complex. Hence, a simpler and more accurate approach is needed for on-site corrosion monitoring to improve productivity. Ideally, this newly developed method should be connectionless so as to address the stringent site safety requirement when monitoring of corrosion status in areas with limited access (e.g. tunnels or structures in operation).
Expected Outcomes
The Challenge Statement Owner is looking for a solution that should fulfill the following specifications:-The corrosion monitoring equipment should be portable in order to ensure accessibility. It should also be able to be operated in a wireless manner (i.e. battery operated) and be rugged enough for field application.-The measurement method which could adopt different techniques such as impedance or electrical pulse should stabilize within minutes to ensure the accuracy of results. The testing technique should not leave behind any visible installations or sampling points.-The system should also be complete with a platform to enable advanced data sharing and communication to enable real time monitoring.
Past Challenge Statement
Reinforcement for Concrete 3D Printing
Challenge Area
Challenge Statement Owners
Current Situation
3D printing with concrete is an emerging technology which could potentially reduce labour and form-work costs, while increasing reliability of concrete infrastructure. Though high in compressive strength, concrete is fairly weak in handling tension. In order to overcome this challenge, concrete is usually reinforced with plastic or metal fibre.
Challenge
Though significant progress has been made in non-reinforced concrete 3D printing, there is limited success in incorporating reinforcements into concrete 3D printing. 3D printed reinforced concrete often has weak material properties due to segregation and non-uniform distribution of added fibre reinforcements. This has prohibited their usage for building and construction application.
Expected Outcomes
The Challenge Statement Owner is seeking for an innovative mechanism or process to incorporate reinforcement into 3D printed concrete. The reinforcement could be added before, during or after the printing process. The 3D printed reinforcement shall comply with the relevant building codes and regulations for building and construction application. The process of addition shall preferably be automated and not too cost prohibitive to implement.
Past Challenge Statement
Autonomous Construction Vehicles and Lifting Equipment
Challenge Area
Challenge Statement Owners
Current Situation
Mass Engineer Timber (MET) is a lightweight material which is preferred to reinforced concrete when constructing long-span structures due to its lifting capacity. However, this still reduces the available crane time needed for hoisting other heavyweight materials on site when lifting and shifting MET components during MET installation.
Challenge
Existing tools which are available that aid in lifting and shifting of MET components are not stable and often require at least 2 workers to operate. This tools still utilize crane, which leaves less crane time available for other activities thereby reducing onsite productivity.
Expected Outcomes
The Challenge Statement Owners are looking for a solution which could improve the efficiency of transporting, lifting and installing MET components. Some of the basic requirements for1. Vertical movement � Sufficient lifting capacity for MET components of up to 4 tons (based on MET density of 500kg/m3, slab dimension 12m x 3.4m x 0.2m)2. Horizontal movement � Sufficient lateral movement capacity, requiring at most 1 worker for transportation of MET within the same floor.3. Reduce crane time for installation, by at least 50% Easy to maneuver and allow great flexibilityin installation height up to 4.5m.
Past Challenge Statement
Use of Recycled Materials for Building and Construction Application
Challenge Area
Challenge Statement Owners
Current Situation
Singapore has achieved success in the use of alternative building and construction materials such as recycled concrete aggregates and washed copper slag for various applications. With the growing emphasis on Circular Economy and Sustainability, a holistic approach is required to close the material loop by optimising material usage during and beyond the materials' lifespan, and containing waste generation by converting various wastes into building and construction resources.
Challenge
If non-Built Environment wastes can be used for building and construction applications, it could reduce the reliance on conventional materials such as sand and granite as resources, and consequently reduce environmental impacts of construction projects.
Expected Outcomes
The Challenge Statement Owner is looking for a proposed solution which should incorporate locally generate wastes to be used as alternatives in the generation of recycled building and construction materials.The product should conform to LTA's Materials & Workmanship Specifications and/or local environmental standards and/or building codes and regulations for non-structural concrete applications. It would be advantageous if the product can demonstrate satisfactory/improved performance compared to conventional building and construction materials. Existing tools which are available that aid in lifting and shifting of MET components are not be stable and often require at least two workers to operate. This tools still utilise a crane, which leaves less crane time available for other activities, thereby reducing onsite productivity.
Past Challenge Statement
Detection and Removal of Foreign Objects From Aggregate Stockpiles
Challenge Area
Challenge Statement Owners
Current Situation
Today more than 90% construction debris is recycled in Singapore. Recycled concrete aggregate (RCA) is generally produced by a two-stage process that involves crushing of demolished concrete and screening and removal of contaminants. Removal of these impurities is a laborious process.
Challenge
Sorting ferrous materials from the aggregate stockpile can be easily picked up or attracted by magnetic screens as they move along the conveyor belt. The challenge is to manually sort out non ferrous materials.Presently, a total of 8 workers are involved in the entire sorting process by visually identifying and manually picking up non-ferrous contaminants from the stockpile. Alternative solution in the market includes eddy current separator that emits a powerful magnetic field to separate
Expected Outcomes
To produce better quality concrete with less reliance on manual labour, the challenge owner seeks an innovative approach
Past Challenge Statement
Early and Comprehensive Underground Service Detection
Challenge Area
Challenge Statement Owners
Current Situation
In various construction projects, underground service detection is crucial as any damage to these services will lead to project delays and stoppages.
Challenge
Among them are critical items such as power cables, telecommunication cables, gas pipes, water pipes, and sewers. Furthermore, serious injury or death to workers can come from striking buried power cables or gas pipelines. Any form of reworking would have to involve various service providers which will increase the cost and time of the project. The accuracy of the existing solutions using electromagnetic (EML) and ground penetrating radar (GPR) is still unable to predict and prevent stoppages. There are varying solutions from various devices and manufacturers, which causes a lack of coherent and integrated system.
Expected Outcomes
The challenge owner is looking for new detection technology for incident and network management.The solution proposed should also take into account the various open source database or public records of underground utilities from other projects in the construction site. Further enhancements through unique collection of information about new underground infrastructure that will help in providing effective detection are preferred by the challenge owners.
Past Challenge Statement
Common Repository for Workable Templates & Objects
Challenge Area
Challenge Statement Owners
Current Situation
The implementation of BIM/IDD is a challenging undertaking for firms that are new to it despite its benefits. Firms need go through steep learning curve to prepare and develop their own templates, objects for typical details like facades, waterproofing and other aspects of construction drawings/models that can be standardised.
Challenge
If the required template is different from that for the BIM e-submission developed by BCA, they would have to develop these templates from scratch which can be time consuming, costly and requires a steep learning curve.
Expected Outcomes
It will be great if typical and workable standardised templates, objects can be developed and shared via common repository for use by the industry beyond BIM e-submission purpose. This will save time and cost and reduce man power.
Past Challenge Statement
Seamless and Self-Propagation Between Design, Engineering and Construction Analytics Models
Challenge Area
Challenge Statement Owners
Current Situation
Architects and engineers involved in the same construction project have two very separate processes. This difference, coupled with human errors within manual processes, leads to a lot of work duplication and inefficiency.
Challenge
Despite the current use of BIM models, changes on both ends are not always reflected; especially if one of the partners or subcontractors within the project is not using the same model. This leads to complications, whereby both parties are unable to fix a problem in the event where there are unreflect changes within the project.
Expected Outcomes
The challenge owner is looking for innovative and smart ways in which changes made in one model could be automatically shared to ensure integrity of models as well as to reduce the manual work, which are prone to human errors and often not done (the self-propagation/integrity parts).
Past Challenge Statement
Effective Management of Equipment Maintanence and Utility Rate
Challenge Area
Challenge Statement Owners
Current Situation
Contractors typically have a sizeable number of assets such as machinery located in various worksites that require periodical servicing and maintenance.
Challenge
Currently, contractors have no real-time visibility on the utilization rate and the exact location of their assets. Typically, workers manually check on the utilization rate of each asset and track these rates on a report.If the assets are under-utilised, having no real-time visibility of where the assets are located does not allow for prompt resource mobilisation between different worksitesPresently, there are alternative IOT solutions, such as on-board diagnostic tools that gather running time and idling speed but the tools are too costly to be mounted on all of the assets.
Expected Outcomes
The proposed solution should include:-Real-time visibility of the assets� utilisation rate for prompt intervention. -Location tracking of the assets for ease of asset mobilisation. -Any device mounted on the assets should be rugged and requires low maintenance, considering the environment of a construction worksite
Past Challenge Statement
Innovative Predictive Planning Solution
Challenge Area
Challenge Statement Owners
Current Situation
Construction planning is a fundamental but challenging activity in the execution of any project.
Challenge
Current ways of developing and managing sequence of activities, schedules, budget, procurement, risks and resource allocation are highly complex, time consuming and not scalable.
Expected Outcomes
Challenge owner is seeking innovative predictive planning solutions that can potentially draw on insights and learnings from past project data points to help planners and quantity surveyors make faster and more accurate decisions in view of achieving greater productivity, quality and profitability in future projects.
Past Challenge Statement
Innovative and Smart Data Depository for Effective Project Management
Challenge Area
Challenge Statement Owners
Current Situation
For project managers, lessons learnt and data points from buying a plot of land to the development of a project are captured and discussed during annual reviews. These data and learning points are often captured by key personnel in emails.
Challenge
Presently, there is a lack of a structured approach to capture data and lessons learnt, making it challenging to access the information. New project managers often have to rely on seasoned project managers for on-the-job knowledge that is acquired through experience. When a senior project manager leaves the organization, these valuable knowledge and insight are often not retained.
Expected Outcomes
To promote knowledge capture and provide easy access to information, the challenge owner is seeking an innovative and smart data repository that will allow project managers to extract relevant data, analyse and generate actionable insights.
Past Challenge Statement
Innovative Tracking and Predictive System for Workplace Safety
Challenge Area
Challenge Statement Owners
Current Situation
Worksite safety has always been a topmost priority especially during the construction phase. Construction workers onsite have a requirement to attend required courses in order to hold the valid licenses to work on specific jobs. Safety officers have to conduct manual checks on personnel equipment and ensure these workers possess valid licenses that comply with safety policies. Despite these safety regulations, incidents at worksites are not uncommon. Some of the incidents involve fall from great height or struck by moving objects such as cranes or forklifts. Furthermore, workers risk being struck by moving cranes or forklifts because of dangerous blind-spots. Today, workers are required to wear personal protective equipment (also known as PPE) when carrying out tasks on site. However, some of these PPEs requirements such as securing the harness to an immobile object to prevent potential falls are neglected. In such a case, workers find wearing the harness cumbersome as they obstruct their movement during the course of work. Although wearing helmets are mandatory on site, workers are prone to dangerous risks in their blind-spots such as being struck by moving cranes or forklifts. The helmet also only protects the users from minor falling objects but does not protect the user for large and heavy
Challenge
Beyond wearing PPEs and having danger awareness, communication and relationship management are critical to convey safety messages effectively. These require quality training and safety professionals to upgrade and enhance their value. As part of the protocol, workers� movement are tracked upon the entry of job site to ensure only certified personnel are working on the jobs. Currently, there is a high dependency on a few key safety supervisors to ensure that sites spanning a large area and involving a large number of manpower, are compliant on safety requirements. Moreover, some of the site locations (such as large infrastructure projects) have difficulty in receiving reception to transmit data, making it
Expected Outcomes
Challenge owners are seeking solutions that can be deployed in a site environment and support the tracking of manpower and their health and safety onsite, as well as monitoring their certifications and equipment onsite. In terms of working safety, the solution should be able to:-Provide warnings to workers and alerts to management (e.g. if worker enters high risk or danger zone, or is not using safety gear, etc.)-Visually identify objects on site and pick up and interpret potentially dangerous situations.In addition, the owners are looking for an effective training delivery using technology such as virtual simulators capturing actual worksite conditions for realistic training. Some of the considerations include low connectivity within a worksite, cost effectiveness, low maintenance, high durability and accuracy. The solution should be able to learn from historical data and allow the main contractors to be pre-emptive and proactive in resolving problems that may potentially arise.
Past Challenge Statement
Improve the Effectiveness of Inspection Process and Quality of Works at Pre-Cast Yard
Challenge Area
Challenge Statement Owners
Current Situation
Today, pre-casters prepare the moulds for precast concrete components including concrete PPVC modules using their interpretation of hardcopy drawings. Once the moulds are completed, the Resident Technical Officers (RTOs) would conduct visual inspection on the assembled moulds with reference to the drawings. The common items inspected by the RTOs include dimensions of the moulds, reinforcement bar sizes, spacing and lapping length, cast-in-accessories, concrete cover, services openings and cleanliness etc.
Challenge
It is often common for the assembled moulds to fail the quality checks due to inaccuracy of interpretation and human errors. This leads to manpower and time loss in rectifying the non-compliant moulds. Furthermore, RTOs may overlook minor details which results in major rectification especially when the precast concrete components have been installed on site. In addition, with precast now being done overseas there are very few or no Resident Engineer (RE) or RTOs who would like to travel to these sites and be stationed there full-time to carry out structural inspection.
Expected Outcomes
The challenge owners are seeking a holistic solution including digital means that is able to improve the productivity and effectiveness of the inspection process as well as the accuracy and quality of works to reduce any manpower and time loss for rectification. Instead of having localized checking inspection, challenge owners are looking for a continuous QA/QCcheck embedded in the process with the new proposed technology or solution.
Past Challenge Statement
Smart Assembly of Rebar Cages
Challenge Area
Challenge Statement Owners
Current Situation
For Prefabricated Prefinished Volumetric Construction (PPVC), modules need to be reinforced with mesh and reinforcing bars (also known as rebars). The steps involved in fabrication and the assembly free-standing volumetric modules are:1. Interpretation of rebar drawings by skilled personnel2. Assembling the mesh and rebar to form a structured cage3. Install the rebar cage into the mould4. Closing of steel mould and installing of services ducts5. Checking and closing of mouldIt requires effort by a 4-man team that takes 8 � 10 hours a day to preparethe rebar cages.
Challenge
It is extremely time consuming process to assemble rebar cages. Moreover, as the interpretation of the rebar drawings are conducted by human, it leaves room for misinterpretation of drawings which means missing rebars and links.If the checks fail (often due to the inaccuracy of rebar drawing interpretation), workers have to amend and rework on the cage all over again. This means more time required to amend the rebar cage.
Expected Outcomes
Challenge owner is seeking innovative solutions to save time and manpower in the fabrication and assembly of rebars. The proposed solution should also boost the accuracy of the rebar cages� structural integrity and greatly reduce unnecessary re-work and save time and manpower in reading/interpretation, fabrication and assembly of rebars.
Past Challenge Statement
Determining Integrity and Durability of Existing Buildings and Aging Structures
Challenge Area
Challenge Statement Owners
Current Situation
Due to the nature of environment and the usage of buildings, existing solutions are unable to accurately determine the condition or reliability of the materials such as steel, reinforced concrete (RC) for the beams, columns and other essential structures that affect structural integrity of a building. Inspection is usually done by a PE (Professional Engineer) through visual inspection periodically, usually in a range of 5 years. Many challenges arise in determining a building structural integrity, one of them is the lack of physical access or unseen parts of the area or structure. Inspection is often limited to visual inspection of accessible areas.
Challenge
Currently, there are a few existing methods in the market that require sensors to be embedded into the structure but this causes other issues such as sensor data reliability and cost effectiveness for sensors to be embedded into all structures.
Expected Outcomes
Challenge owners are looking for a solution to improve and simplify the inspection process and provide reliable measurable data that is low cost and can be implemented on existing buildings. These data can be in the form of and not limited to yield strength, corrosion of reinforcement, strain, crack width and etc.Early indications can help determine if building should be decommissioned or strengthened or rectified to ensure overall safety
Past Challenge Statement
Smart Inspection Platform
Challenge Area
Challenge Statement Owners
Current Situation
Before a building can be occupied, it is important to carry out regulatory site audit checks to ensure that the building is in accordance with the approved plans (e.g. BIM models) and compliant with the Building Control Act and Regulations. MEP (mechanical, electrical, plumbing) systems need to be installed according to the specifications or drawings. It is also critical for code compliance, such as fire safety. During the regulatory inspection, the activities that an Inspecting Officer carries out include travelling to and fro from the site, site walk with the project team, manual measurement-taking using various equipment, photo- taking and documentation work.
Challenge
-Inspection activities are labour intensive and time-consuming. -Other inspection challenges arise from MEPs located in confined or unreachable spaces. Due to these challenges, there is no common measurable parameter to indicate if the particular installation was done incorrectly or beyond the required specifications. -Efficiency and accuracy of inspection activities by qualified personnels, project teams as well as authorities is important.
Expected Outcomes
The challenge owner is looking to achieve greater efficiency and accuracy of regulatory site inspection through proven technologies:-Digitize and transform inspection processes by tapping on 3D scanning, robotics and BIM technology to capture site data for assessment and detect non-compliances. -Empower the industry to conduct their own as-built regulatory check on parts of the building project once completed. -Solution must be able to take accurate site measurements for evaluation.
Past Challenge Statement
Innovative Predictive Solution for Building Maintanence
Challenge Area
Challenge Statement Owners
Current Situation
Energy accounts for a significant part of operating cost for commercial buildings. Currently there is no holistic data on the overall health status of buildings. Energy efficiency of equipment (i.e. chillers) deteriorates with age, and a lot of energy will be wasted by the time routine maintenance detects and fixes the problem.
Challenge
Besides being manpower-intensive, there are fragmented data, systems and multi-vendors to manage within a building. These issues coupled with a lack of relevant and live system data, makes it challenging to predict building and system failures. Currently, there exists a variety of energy efficient solutions in the market such as using inputs that positively correlates with fault for e.g. harmonics (i.e. measurement of vibration from equipment), electrical current etc. However, many are too cost prohibitive for adoption by commercial/non- industrial real estate.
Expected Outcomes
The challenge owners are seeking innovative solutions that will help:-Gather holistic and relevant building data to enable accurate predictive monitoring e.g. predict system failure and prescriptive monitoring e.g. algorithms embedded to advise the next course of action/recovery to reduce building disruption and man effort. -Measure a variety of outputs by building equipment (e.g. chillers, HVACs and etc) that have greater risk of failure so as to prescribe timely maintenance/fixes. The solution needs to be able to measure outputs with an analytics tool, prescribing maintenance/fixes with low false positive rates to maintain equipment and cost efficiency. -Generate appropriate responses and action plans, suggest various ways to conduct better training and refresher programmes, as well as test and certify readiness of maintenance staff.
Past Challenge Statement
Innovative Solution for Building Façade Cleaning, Inspection and Diagnosis
Challenge Area
Challenge Statement Owners
Current Situation
Maintenance of the building fa�ade is a labour intensive and dangerous activity. Due to aging building stock and the increasing complexity of fa�ade design, it is necessary that building fa�ades are regularly cleaned, inspected and maintained to ensure safety.
Challenge
Current practice of fa�ade cleaning involves a skilled professional with existing equipment of gondolas and ropes. Despite safety training and preventive measures, it is still a high risk activity which translates to higher labour cost. To ensure effective inspection, the building professionals (e.g. Professional Engineers, Registered Architects, Resident Engineers, Resident Technical Officers, Professional Cleaners etc.) are also required to work at heights to carry out close range inspection. Such method of cleaning and inspection is often laborious and prone to fatigue and human errors. There may also be areas that are difficult for humans to access.
Expected Outcomes
Proposed solutions should either enhance or provide an innovative alternative to the existing methods. Reducing risk and effectiveness of existing methods is imperative. The proposed solution may consider the following:-Intelligent inspection software system to recognize building defects through data analytics based on data collected during the inspection. -Introduction of robotics is an alternative, but proposed solution should consider sustainability and reliability for various facades (concrete, glass and metal) and environments. Solution should be capable of manoeuvring around building envelopes, including those with irregular profile, easily and safely to clean the facade. -Design consideration is another aspect that should be looked into, for instance, solutions should be able to assist architects and designers to take into account maintenance of the building fa�ade. This translates into savings by improving a building's life cycle cost and reduce cost required for facade cleaning and maintenance.
Past Challenge Statement
Better System Integration For Facilities Management
Challenge Area
Challenge Statement Owners
Current Situation
Today, the management of tenant feedback are manually recorded. Information flow may be delayed and conveyed to the wrong technician/vendor for corrective actions. Tasks involving multiple processes and departments have to be done manually.
Challenge
Departments are sometimes unsure of the subsequent processes to follow up or if they are indeed responsible for the tasks, causing further delays or tasks being left unattended to.The process of verifying and following up with the vendor on manpower shortages with the absence of site staff responsible for them is also time consuming. When paper-based service reports need to be brought back from site for compilation before following up with finance for payments, service to payment cycle is again delayed while documents risk getting misplaced at site or on the move.
Expected Outcomes
To achieve greater customer satisfaction, the challenge owner is seeking innovative solutions to help their facilities management team to efficiently manage service requests from initiation, to coordination of remedial actions/tasks between technicians/vendors, departments and processes, as well as track progress to ensure timely resolution.
Does your company have a
challenge statement to contribute?