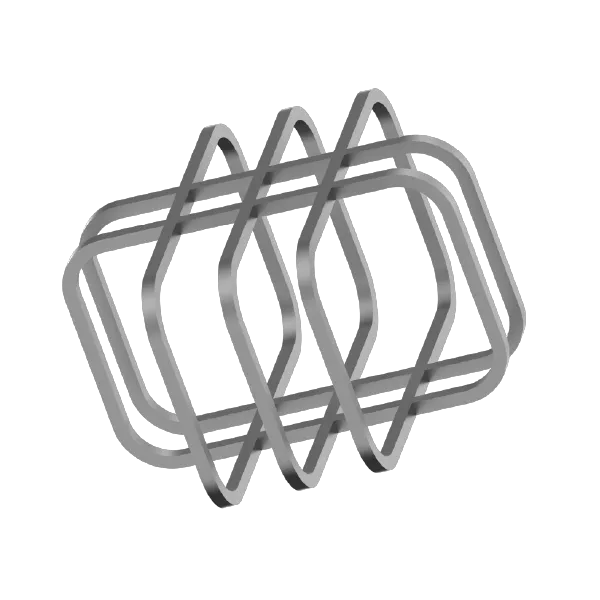
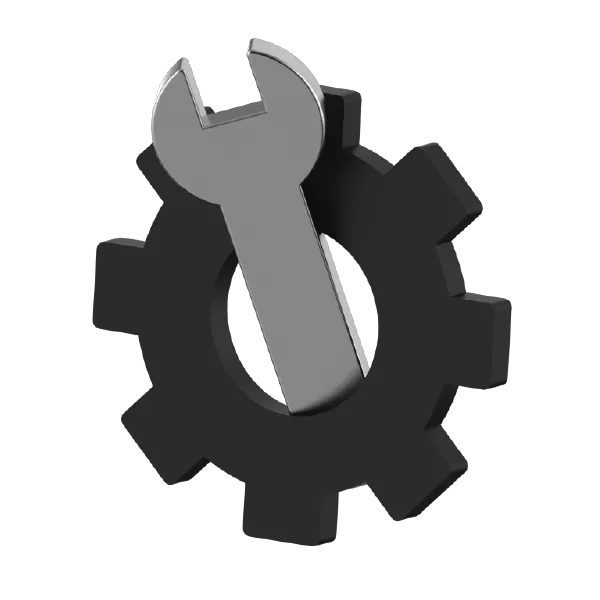
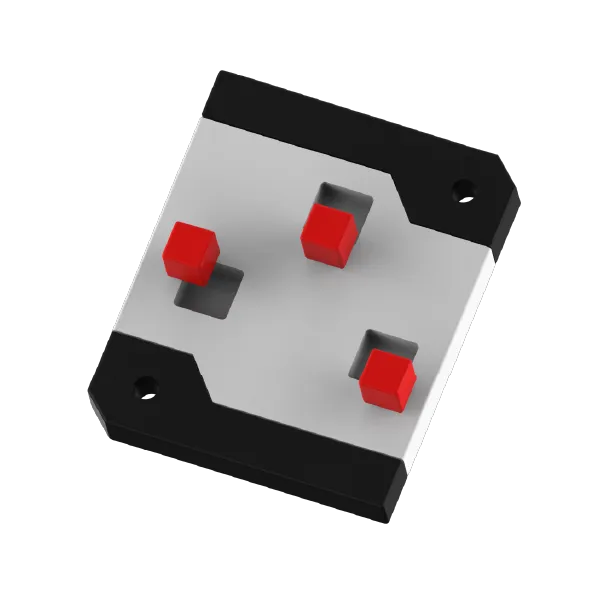
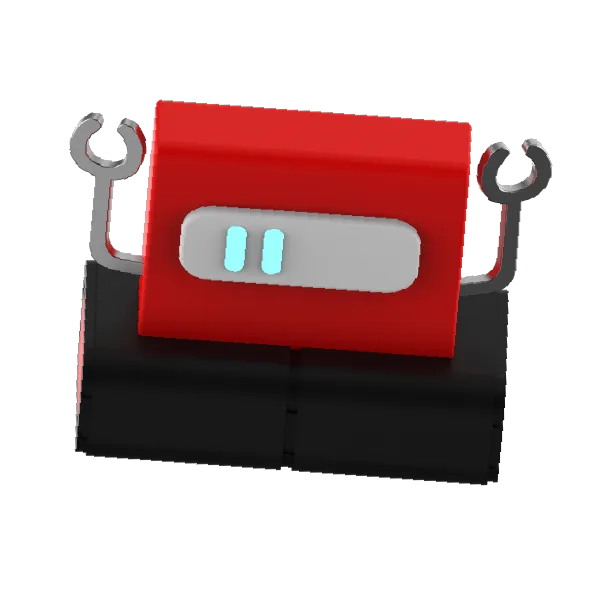
Building Inspection, Maintenance and Facility Management
Automated Quality Inspections for Building Interiors
Challenge Statement Owner:
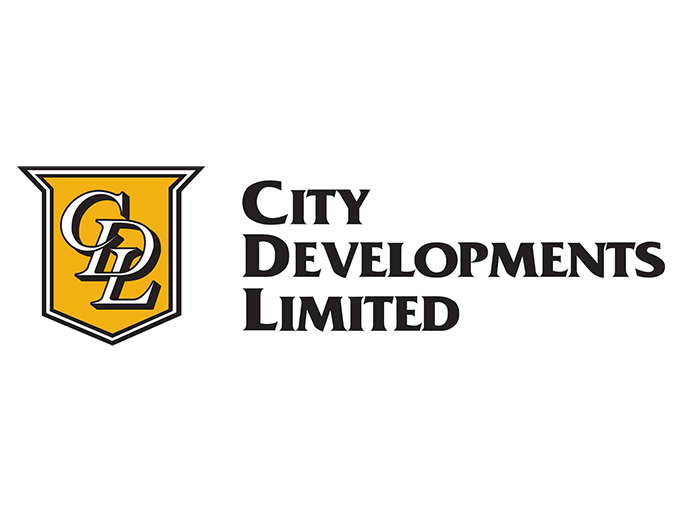
City Developments Limited (CDL), headquartered in Singapore, stands as a leading global real estate company with a robust legacy dating back to its establishment in 1963. Renowned for its commitment to excellence and innovation, CDL has been instrumental in shaping urban landscapes through a diverse portfolio of developments spanning residential, commercial, hospitality, and integrated projects. CDL's success is rooted in its ability to adapt to market demands, delivering high-quality and sustainable solutions that reflect cutting-edge design and technological advancements.
Background
CDL’s residential projects are well regarded due to their high quality. This can be attributed to strict and robust quality assurance (QA) and quality control (QC) checks conducted before the handover of each project. These processes are designed in-house, tapping on a wealth of experience and information from past projects to ensure that the execution of the inspections is continually optimised.
Following BCA’s quality mark (QM) inspection, CDL’s quality inspector (QI) and customer service (CS) teams take over the residential units to carry out aesthetic and functional checks, in preparation for the handover to the home owners.
Most projects require inspection of a large number of residential units (600 to 800 units) over a short period (up to three months). The inspections are highly dependent on the speed of preparation by the main contractors. Hence, the time pressure on both the QI and CS teams to conduct their inspections is very high.
The QA/QC inspection process is done visually by CDL inspectors, who then record defects onto a digital platform. However, there is a dwindling number of personnel who have enough experience and knowledge to be effective in doing these inspections, as this workforce ages and younger staff prefer other roles. Therefore, alternative methods of QA/QC inspection will have to be developed.
The Challenge
CDL is looking for a solution to automate the interior inspection at residential projects.
Requirements
The solution should:
- Using a high resolution 360° camera or similar device, detect and identify visual defects that are visible to the naked eye (including, cracks, chips, scratches, stains, peeling paint, rust etc.)
- Accurately identify and categorise at least 70% of the detected defects;
- Complete the inspection of a single residential unit between 10 and 15 minutes (compared to the approximate 45 minutes taken by by 2 human inspectors);
- Be integrated with a digital platform, which can be pre-existing or specially developed to support your solution;
- Automate the process of flattening the images;
- Generate a full defect report for a single residential unit within 48 hours;
- Build up a database of defect images to help train the AI model to achieve higher accuracy; and
- Provide suggestions to optimise the QA/QC inspection process.
Proof-of-concept (POC)/Pilot Support
CDL has identified 2 residential project sites (nearing TOP in 2024) in Singapore for test bedding.
The POC project will be supported by representatives from the CDL Quality Inspection and Customer Service teams.
CDL will provide up to S$50,000 to support future adoption of the solution over an estimated period of 6 months.
They are willing to work with early-stage solution providers on a proof-of-concept. If successful, they would be keen to work towards commercialising the solution.